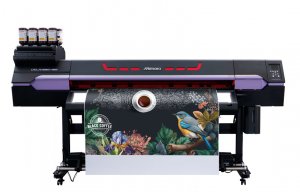
Mimaki celebrates 20 years in Amsterdam
Orders now in place for second and larger machine announced in August 2023.
19th January 2024
Innovation in Textiles
|
Diemen, Netherlands
Mimaki Europe reports that its first DTF (direct to film) printer, the TxF150-75, has surpassed the milestone of 300 units sold across the EMEA region since its launch in February 2023.
The wide-spread adoption of the TxF150-75 not only demonstrates the quality of the printer, but also the rising popularity of the DTF printing method.
The TxF150-75 offers a solution to common DTF issues, such as poor ink ejection and white ink clogging, through its built-in circulation system and degassed ink pack. Alongside other Mimaki core technologies, such as the nozzle check unit (NCU) and nozzle recovery system (NRS), the TxF150-75 provides an efficient printing process with minimal need for intervention, filling the gap in the market for a stable, reliable DTF solution.
Impact
DTF is the process of digitally printing directly onto a special transfer film sheet. The printed film is subsequently sprinkled with a hot-melt powder and heated. Once the transfer sheet is cured and dried, it can be heat-pressed onto a variety of fabrics to create premium transferred designs for customised merchandising, sportswear and an array of other promotional applications for the textile market.
With traditional screen printing, the plate creation required is far too time-consuming and also does not match DTF’s ability to produce vivid colours and quality details such as shapes, lettering and motifs – often sought after in the promotional and merchandising space for bespoke textiles.
“We’ve seen the impact DTF is having on the market in recent years and wanted to offer a solution that excelled in usability, reliability and quality,” said Arjen Evertse, general sales manager for Mimaki Europe. “The Tx150-75 provides all of these benefits, but its popularity is also due to its suitability for those introducing DTF technology to their production capabilities or those who already have an in-house business producing smaller run jobs.”
Meanwhile, over 100 orders have already been secured for the TxF300-75 which has all the same capabilities of the TxF150-75 but a maximum print speed that is three times faster and was only announced in August 2023.
“We are seeing significant interest in this system, especially among established DTF application suppliers who are printing high volumes,” said Evertse
Impact
DTF printing has had a big impact on the apparel industry due to its versatility to print on a range of materials and the quicker delivery times achievable compared to other printing processes.
At 80cm in width, both Mimaki DTF models are 20cm wider than the industry standard. This extra width is matched by the Adkins post-press powder shaker cure system, ensuring customers have a complete DTF solution that can print larger garments with less waste and quicker production times, allowing for a more cost-effective process.
Mimaki has also created its own range of Oeko-Tex Eco Passport certified water-based pigment inks (PHT50) especially for this solution.
“The response to our DTF products in the past year has been fantastic and we are confident that adoption of these technologies will only accelerate from here,” Evertse concluded. “We look forward to supporting our customers and the market as it transitions to trusted, reliable DTF solutions.”
Business intelligence for the fibre, textiles and apparel industries: technologies, innovations, markets, investments, trade policy, sourcing, strategy...
Find out more