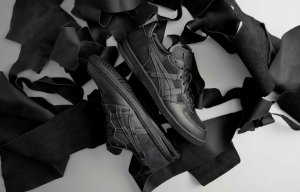
Asics range from steering wheel waste
Activated functional yarns allow process steps to be eliminated.
14th June 2021
Innovation in Textiles
|
Reutlingen, Germany
Karl Mayer Stoll and Desma Schuhmaschinen, headquartered in Achim, Germany, are involved in a joint project to make processes faster and save on labour in the shoe industry, which like the fashion sector is driven by short collection cycles and enormous pressures in terms of time and cost.
The two partners believe that combining their specialisms at every stage of the shoe industry’s global value chain is an opportunity that promises plenty of potential for optimisation.
They have jointly developed an integrated solution that starts with the production of seamless 3D-knitted uppers, which are then hardened in order to activate the functional yarns woven into them, before being attached directly to dual-layer sole constructions.
This minimises lead times in the development and production process and allows the machine settings to be adjusted for optimum product quality without any additional investment.
The machine technologies used for the process – Stoll flat weft knitting and Desma direct sole attachment technology – are already in widespread use in the shoe industry.
Most significantly, the new solution reduces the number of time-consuming production steps required, such as making up the uppers and manually joining together uppers and soles made from different components. It is also a sustainable innovation, because the seamless manufacturing technique means there is no scrap or waste. In addition, a seamless, 3D-knitted upper is more comfortable to wear, being shaped to provide the perfect fit.
Productivity and pioneering design considerations have also been factored into the process and it is now possible to manufacture high-performance footwear with custom designs using industrial processes.
“This shoe model provides the perfect example of how we can manufacture complex products with a high degree of efficiency and sustainability, by working together and harmonising our process sequences,” says Andreas Schellhammer, head of Stoll.
The footwear is manufactured using the ADF 330-32 ki BcW flat weft knitting machine, which like all ADF machines interacts with a number of different knitelligence components to provide an efficient, automatic and fully digitalised production process.
It can also handle a huge variety of different designs. With technology such as inverse plating, Stoll-ikat plating and Stoll-weave-in, it can incorporate a wide range of knitwear looks and all the components of the upper directly into the fabric, speeding up the making up process.
Design potential can be expanded even further by using the multi-gauge E 9.2, in keeping with current trends in the textile shoe upper market.
The fabrics created using this process boast designer textures with a level of detail never seen before in flat weft knitted uppers and with on-trend non-porous surfaces, The textures of the stitching in the fabric are almost imperceptible.
Business intelligence for the fibre, textiles and apparel industries: technologies, innovations, markets, investments, trade policy, sourcing, strategy...
Find out more