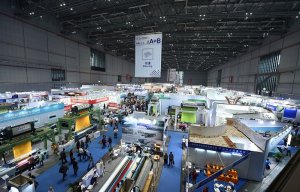
New dates for ITMA Asia + CITME 2018
The company’s Power-Shrink rubber belt compacting line is designed to allow sanforizing and compacting of very different types of woven fabrics.
14th September 2016
Innovation in Textiles
|
Leonberg
Brückner, a leading German textile machinery producer, will exhibit its new developments and products for the woven fabrics sector at this year’s ITMA Asia + CITME trade fair that will take place from 21-25 October in Shanghai, China.
A leading family-owned producer of textile finishing lines, Brückner supplies consulting services and lines for almost all purposes in the field of textiles, technical textiles, nonwovens and floor coverings. Brückner offers sanforizing lines, continuous dyeing lines, infrared dryers, relaxation dryers, compactors and stenters for coating, drying and heat-setting. This year in Shanghai, the company says it will present an extensive and varied programme.
The company’s Power-Shrink rubber belt compacting line is designed to allow sanforizing and compacting of very different types of woven fabrics. Finishing on a sanforizing line is said to give the fabric a more stable structure, silky shine, smooth handfeel and minimum residual shrinkage values.
Typical end products are apparel fabrics for shirts, trousers, jeans and workwear, as well as fabrics for bed linen, home textiles or upholstery materials. Brückner offers single or double sanforizing lines and combinations with felt calenders depending on the product and the customer’s requirements.
With a continuous Power-Colortherm dyeing line by Brückner, the customers can achieve uniform and reproducible dyeing results, the company reports. The lines are said to ensure a crease-free fabric flow without shading and migration.
The symmetrical structure of the air circulation zones aims to prevent a different shade on the two fabric sides. In addition, the installed power is adapted to the low air flows required for dye drying, which leads to a considerably lower energy consumption, according to the company. Typical end products dyed on Brückner lines include fabrics for shirts and trousers, working clothes and home textiles.
With continuous research and development efforts, the company aims to make its machines even more efficient, increase their service life and support the customers in minimizing their ecological footprint.
An indirect gas heating system has been developed particularly for the finishing of knitted fabric, which is designed to save energy in combination with a special heat-recovery system and prevent the yellowing of the fabric.
“This is of particular importance in case of sensitive fabric containing elastane,” the company explains. “If a company does not want to invest in a completely new line, Brückner offers a modification of the heating system for example from oil to indirect gas heating.”
Brückner also developed a new minimum application unit, which works with a minimum liquor tank of around 2.5 l for each m of working width. The minimum application quantities require less water evaporation in the following processes (for example drying or curing), which is said to have a positive effect on the energy requirement at the respective dryer.
In addition, there is no waste or prodigality of chemicals and no expensive disposal is required since the contents of the liquor tank can be used almost completely, the company reports.
Business intelligence for the fibre, textiles and apparel industries: technologies, innovations, markets, investments, trade policy, sourcing, strategy...
Find out more