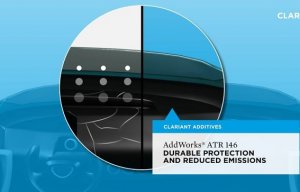
New additive solution for smoother fibre production
Exolit OP 560 is a reactive FR that eliminates unwanted emissions since it becomes chemically bonded within the polymeric polyurethane foam structure.
10th October 2014
Innovation in Textiles
|
Muttenz
In its draft Alternatives Assessment report on flame retardants in flexible foam, the US Environmental Protection Agency (EPA)has identified Clariant’s oligomeric phosphonate polyol (OPP) flame retardant Exolit OP 560 – as a safer alternative to pentabromo diphenylether (pentaBDE), traditionally used for giving fire protection to foam.
The report is part of the EPA’s Design for the Environment programme, which helps industries choose safer chemicals, and offers a basis for future decision-making by providing a detailed comparison of the potential public health and environmental impacts of chemical alternatives.
“Exolit OP 560 is not only halogen-free but becomes an integral part of the PU foam, creating possibilities to produce flexible foams with locked-in fire protection without the environmental and health concerns of traditional flame retardants,” said Adrian Beard, Head of Marketing Flame Retardants, Clariant. “The US-EPA report is a step forward in easing the identification of safer alternatives by PU foam producers and end-users.”
Exolit OP 560 is a reactive flame retardant that eliminates unwanted emissions since it becomes chemically bonded within the polymeric polyurethane foam structure. As a result, the Exolit OP 560 cannot leave the foam during use.
Exolit OP is also halogen-free, and is said to have a more favourable toxicological and environmental profile. It cannot bioaccumulate in humans and other organisms since it is locked into the foam, the company reports.
Further benefits for PU applications are said to include great ageing stability, as well as low smoke density and smoke gas corrosivity in case of a fire. The phosphonate’s high effectiveness and good compatibility with natural polymers allow it to be used at low dosages in the foam matrix, which also adds to the foam’s excellent sustainability profile.
Natural Foams Technology (formerly Green Urethanes), the provider of green solutions to the PU industry, has confirmed that manufacturers can use Exolit OP 560 with its natural oil polyol (NOP) foams to develop low-emission flexible foams that meet internationally accepted flammability standards.
These include TB117-1975, California’s open flame flammability test for upholstered furniture, and the updated Cal TB 117-2013, which comes into force in January 2015.
With high bio-renewable content, the foams have become the first to be accepted into the USDA’s BioPreferred programme, a US federal programme to encourage industry to switch to more sustainable materials.
NCFI Polyurethanes, a North Carolina-based manufacturer, has been using the NOP technology in their BioLuxMax line for several years. After running extensive trials with Exolit OP 560, they plan to introduce a commercial product in the fourth quarter 2014.
“This is a natural evolution for our BioLuxMax initiative,” said Chris Bradley, VP of Consumer Products for NCFI. “This project has always been about maximising the benefits we can offer our customers. We feel a foam with 33% certified bio-renewable content that passes the open flame standard of CA-117-1975 and can be labelled under the new California law as flame retardant free, is a huge step in that direction.”
Business intelligence for the fibre, textiles and apparel industries: technologies, innovations, markets, investments, trade policy, sourcing, strategy...
Find out more