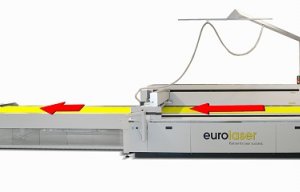
Laser cutting of filter materials at Filtech 2019
Opinion
As evidenced from the Filtech 2016 exhibition and conference held in Cologne, the size and number of pores in a filter fabric dominate design considerations.
19th October 2016
Adrian Wilson
|
Cologne
At the Filtech 2016 exhibition and conference held in Cologne, Germany, from October 11-13, Jürgen Hanel, head of technical textiles finishing machinery specialist Monforts, remarked to me that when it comes to filter media, the key concern is not so much with the properties of a fabric, nor the fibres holding it together, but rather, the holes between those fibres in the fabric.
I hadn’t thought of it that way before, but it’s an easy way to nutshell many recent developments – the size and number of pores in a filter fabric dominate design considerations.
Nanofibres, for example, are all about creating much more surface over a given area, but in filter industry terms, it’s so that many more holes can be accommodated, to trap more and ever smaller particles.
The addition of nanofibre layers was a key theme at Filtech 2016, as evidenced by the latest products from nonwovens companies such as Ahlstrom, Donaldson, Hollingsworth and Vose, JX Nippon, Mann and Hummel, Neenah, Nxtgen, Porex etc.
Similarly, pleating is again about creating more surface space over a given area, in which to make more and increasingly smaller holes.
An interesting product here is the the Solaft StarBag promoted by Italy’s Testori, which can considerably reduce costs and solve bag house capacity problems. The filter’s pleated design doubles the available filter area in the same space as a traditional cylindrical or oval bag. The pleats are gathered at the top snap band so that the filter can fit in the same cell plate hole as a standard bag and horizontal bands sewn into the needlefelt, in combination with the frame, ensure it retains its pleats for its entire service life.
The pleating machinery business is becoming very competitive. Joining established players in this technology field such as Swiss-headquartered JCEM and India’s A2Z in Cologne this year, was Roth Composite Machinery, headquartered in Steffenberg, Germany, formed from the merger of two well-known companies, EHA and Schlesinger. As part of Roth Industries with 1,100 employees, this new company can draw on the know-how and expertise from other business areas in filament winding and prepreg equipment for composites, as well as production machines for brushes and brooms, and involve 30 in-house design engineers in its projects.
Getting back to the subject of holes, Haver and Boecker, based in Oelde, Germany, is a manufacturer of woven wire fabrics and has developed a way of getting twice the number of pores into a square metre than is available from traditional weaves. The company has now adapted its in-house traditional weaving looms in order to do this at industrial production rates.
Haver and Boecker’s vice-president of sales, Friedrich Edelmeier, explained that the company’s RPD Hiflo-S woven mesh material can achieve twice the throughput volume flow for a given pore size than traditionally woven materials, as a result of its 3D structure.
“We have been able to optimise a 3D structure by separating the weft wires from one another so that the number of pores is doubled over a given surface area, but the pore size remains the same,” he said.
The company developed this technique with the assistance of the Math2Market GeoDict simulation system.
“The traditional way of designing and testing filter prototypes is costly and time consuming,” said Andreas Wiegman, CEO of Math2Market, which is based in Kaiserslauten, Germany. “This is due to the complex interplay of the material properties of the filter media, the arrangement of fibres in the medium, the physical and chemical properties of the fluid being filtered and the characteristics of the particles in the fluid. GeoDict is a modular package developed for the simulation of filtration processes and its modules help gain insights into the behavior of existing filters, and beyond that, to develop new filter media.”
That may sound like a little more than just considering holes, but even keynote speaker Professor Gerhard Kasper, of the Karlsruhe Institute of Technology delivered a highly technical speech that in essence boiled down to either maximizing them, or sealing them.
Better filter media are not the only answer to an efficient filtration plant, he explained, talking specifically about the process of gas cleaning with pulse-jet filters.
Unwanted holes are just as critical, it seems, as those specifically engineered into filter fabrics.
“PTFE-coated membranes are very sensitive and prone to leakage, but it’s not just in the fabrics,” Professor Kasper explained. “Leaks from filter bags are transient, but those from elsewhere are continuous. In a well-maintained unit, fifty per cent of leaks are down to the hardware of filter systems – the gaskets and welds and seams – and in old plants much more than that. It’s where the majority of leaks are coming from.”
There was much more to Filtech than just holes, of course. This year, the conference comprised 174 papers presented by speakers coming from 23 countries and attracted around 40 new companies to swell exhibitors to a new record of 355.
Business intelligence for the fibre, textiles and apparel industries: technologies, innovations, markets, investments, trade policy, sourcing, strategy...
Find out more