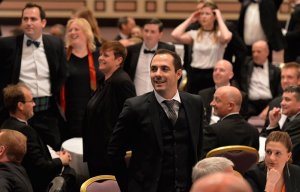
UK composites industry celebrates latest achievements
The Innovation Awards were presented during the 3rd International Composites Congress (ICC) this month at the International Congress Center Stuttgart.
28th September 2017
Innovation in Textiles
|
Frankfurt
The German Federation of Reinforced Plastics (AVK) has announced the winners of its three prestigious Innovation Awards to institutions, companies and their partners in the composites industry. The Innovation Awards were presented during the 3rd International Composites Congress (ICC) this month at the International Congress Center Stuttgart. The award winners presented their innovations to the international audience during the trade fair.
“Every year, we are astonished by the level of innovation demonstrated by the research and development departments of companies and institutions in our sector. They are making an important contribution to achieving even greater sustainability and efficiency,” commented Dr Elmar Witten, Managing Director of the AVK.
BASF SE, with its partner company Sonae Arauco, became winners in this category with their 3D Mouldable MDF – A new dimension for the furniture industry. The new binder technology is designed to enable manufacturers to make 3D moulded furniture parts cost-efficiently. Industrially manufactured wood products are normally used as panels, e.g. particle board, medium-density fibreboard (MDF), oriented strand board (OSB) or plywood. Until now, curved or moulded parts have rarely been made using these materials. The innovation presented by BASF SE and its partner aims to provide a new wood material for the furniture and interior design industry.
The two companies have developed a thermally mouldable composite, which can be processed into an intermediate product using existing panel production equipment. This can then be stored for a long period and later moulded into 3D components or stamped with a structured, decorative design.
Together with Sonae Arauco, BASF SE has developed a stable MDF panel, which can then run through the complete industrial process without the need for additional technical changes to equipment. The major advantage of the product is that it can be moulded simultaneously in all three spatial axes. The simplification of the process and shorter pressing times also increase productivity significantly. The product’s improved moulding properties enable designers to create a wide range of new forms and styles.
Audi AG and its partner Secar Technology were recognised for One Shot Technology. Developed by Audi AG, the technology directly combines continuous fibre-reinforced profiles with short fibre reinforced moulding material. The component is made without the use of additional adhesive.
“It enables manufacturers to integrate reinforcement in specific areas to optimise mechanical performance. Areas with the highest properties can now be combined with others featuring significantly reduced properties in a single component. The profiles are manufactured in a pultrusion process and offer outstanding mechanical properties at a moderate cost,” the company explains.
In addition, the process is said to offer efficiency gains, e.g. by eliminating the need for joining technology. It is ready for use in series production and a type approval certificate is available.
Aachen Center for Integrative Lightweight Production (AZL) at RWTH Aachen University and its partner companies BMW AG, KraussMaffei Technologies, Arges, Precitec, Sensortherm and Zeiss Optotechnik became winners in the Research Science category. The innovation, called Photonics-enabled process chain for manufacturing functionally integrated thermosetting/thermoplastic hybrid components for automobile construction, is the result of research conducted under the leadership of the AZL since 2014.
For the first time, the project has been able to combine thermosetting and thermoplastic FRP using a technique suitable for large series automobile production. The process chain developed by the partners enables manufacturers to produce continuous fibre-reinforced hybrid plastic components for the automotive sector.
The potential savings in material and operating costs throughout the process chain are around 20%. This new technology can be used to implement new component concepts. For example, BMW has already redesigned part of the structure of the i3. As well as applications in the automobile sector, the technology is also suitable for producing components for other sectors, e.g. mechanical engineering and plant construction, energy and environmental technologies.
Business intelligence for the fibre, textiles and apparel industries: technologies, innovations, markets, investments, trade policy, sourcing, strategy...
Find out more