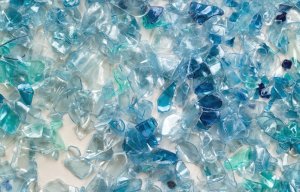
New technology for production of BCF yarn from recycled PET
The cooperation covers BCF (bulk continuous filament) lines which produce carpet yarns by spinning recycled polyester or blends of virgin PET chips and recycled flakes.
16th August 2016
Innovation in Textiles
|
Egelsbach
After having worked successfully together during the past year, Trützschler and plastic recycling systems specialist EREMA have signed a cooperation agreement in the area of recycled materials and especially of R-PET. The cooperation covers BCF (bulk continuous filament) lines which produce carpet yarns by spinning recycled polyester or blends of virgin PET chips and recycled flakes.
The overall spectrum of products offered includes a Vacurema Basic Line and secondary components from EREMA which feed the inline connected symTTex spin positions of Trützschler Man-Made Fibers with a high-quality polymer melt.
For cost reasons, recovered secondary raw materials, such as flakes from used PET bottles, have long been a popular commodity in both the plastic and in the fibre industry, Trützschler reports. Since the quality of the raw material plays a decisive role when spinning thermoplastic polymers, the bottle flakes have to be treated with special care, the company explains.
EREMA’s Vacurema technology offers modular solutions with a vacuum reactor, a directly connected single-screw extruder and a high-performance filter for this process step. The high quality of the melt with respect to viscosity (IV value) and purity lays the foundation for top-quality filaments. The upstream processes have little impact on the directly following spinning process, since only small pressure fluctuations occur during backwashing or screen changes, the company clarifies.
Trützschler says its R-PET-spinning technology is based on the proven system components for spinning primary chips. The process involves its well-known spin packs and the double-shell godets, the HPc-texturing system and the fully automatic winder.
“Existing customers will appreciate the use of the same key components for operation of the R-PET plant. The support of process and product development for recycled polyester through process engineering in Winterthur is part of the package,” Trützschler says.
Last year, Trützschler and EREMA jointly developed a carpet yarn plant for BCF yarns from recycled PET on customer demand. While the reactor, the extruder and the polymer filters were delivered by EREMA, Trützschler Man-Made Fibers was responsible for spinning, drafting and winding. The companies say that the plant is very flexible, so that both yarns from 100% recycled material or blends with PET primary granules can be spun. The BCF yarns are used for various applications.
With about 3000 employees, Trützschler is one of the world's leading textile machinery manufacturers. The company specialises in machines, installations and accessories for spinning preparation, the nonwovens and man-made fiber industry. The headquarters of the 125+ year old company is located in Mönchengladbach, Germany and its subsidiaries Trützschler Nonwovens & Man-Made Fiber GmbH with two production sites, and
Trützschler Card Clothing GmbH, are also located in Germany. Sites in India, China, Brazil, USA and Switzerland, as well as a number of service centres, provide customer proximity in the important textile processing areas.
Since November 2012 Trützschler Switzerland AG in Winterthur has been bundling decades of experience in development, design and construction of spinning lines for BCF as well as industrial yarns for technical applications as a center of competence.
Since it was founded in 1983, EREMA Engineering Recycling Maschinen und Anlagen Ges.m.b.H has specialised in the development and production of plastic recycling systems and technologies for the plastics processing industry and is regarded as the global market and innovation leader in these sectors. EREMA’s technology has become established as a leading global standard for a wide variety of recycling tasks, ranging from the recycling of polyolefins to polyester (PET).
Around 480 people around the world work for the Austrian group. With its own sales and service companies in the USA and China, plus around 50 local representatives in all five continents, EREMA provides custom recycling solutions for international customers. Innovative technology and global service support additionally ensure that owners enjoy the maximum benefit from their EREMA systems.
Business intelligence for the fibre, textiles and apparel industries: technologies, innovations, markets, investments, trade policy, sourcing, strategy...
Find out more