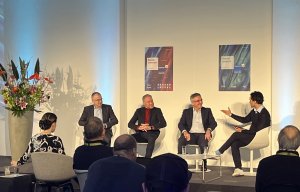
Fully digital focus in Frankfurt
In the build-up to the Texprocess show in Frankfurt this May, Innovation in Textiles caught up with the VDMA’s Elgar Straub.
13th March 2017
Innovation in Textiles
|
UK
In the build-up to the Texprocess show in Frankfurt this May, Innovation in Textiles caught up with the VDMA’s Elgar Straub.
As the managing director of the VDMA’s new Textile Care, Fabric and Leather Technologies division, how is Germany’s sewing and garment technology industry doing at present?
Elgar Straub: Very well indeed. Between January and November 2016 – the latest figures we have – the sector’s export sales were up 11.7%, the highest growth for many years. This follows export sales of German sewing and garment technology of €523 million in 2015. The USA is by far the biggest customer for German garment and sewing technology by far, followed by Poland, Italy and France.
What about the current UE28 trading block as a whole?
ES: In 2015, the block’s exports of sewing and garment technology were worth around €1.327 billion, with the USA again the biggest destination market, followed by China and Turkey. Sales to China were worth more than €95 million, and those to China over €65 million. There has been considerable investment by the US car and aerospace industries in German technology for technical textiles in recent years, but also the US garment and clothing industry has been bringing production back. This started long before the recent political changes, three or four years ago. Wal-Mart, for example, has invested between $5-6 billion in new production lines in the USA as part of its initiative to source an additional $250 billion in products made, assembled or grown in the USA in the years up to 2023, and there have also been initiatives by sports brands such as Under Armour.
It’s all very connected to so-called Industry 4.0 and perhaps the biggest trend is that of individualization.
Can you elaborate?
ES: There’s an enormous demand for individual products across many industries and this will continue. Take the car industry, for example. We’re now seeing serial production in low batch sizes which means that in any one year, there might only be three or four cars that are identically the same in a production of two or three-hundred thousand. And this is possible as a result of new technology. The same principles are being applied in the clothing and footwear industries, and we’re seeing the establishment of microfactories by some of the big sports brands like Adidas and Nike – as well as smaller companies – who are taking a keen interest in establishing small-scale, highly flexible manufacturing operations in order to be nearer to their customers.
In other words, so-called ‘reshoring’ to high wage countries where it hasn’t been practical to manufacture commodities for many years?
ES: Yes, it’s an entirely new type of manufacturing structure that’s emerging, involving the digital integration of design, processing and logistics for both clothing and technical textiles. But we’re not looking at commodities, but higher-priced individualised items. We’re talking about a very high level of automation, shorter reaction times and high flexibility, with the setting up of joint databases and data security systems. There will be data maintenance along the whole value chain, enabled by Cloud solutions.
So this isn’t the return of conventional manufacturing as it’s generally conceived is it?
ES: No, it’s going to require different skill sets altogether and networked people and systems will be making collaborative decisions. It involves a basic change to the way work has to be structured and the challenges posed by systematic thinking and multi-disciplinary collaboration will be intensified. There will still be low-skilled jobs in these environments, but the advantage will be that the machines will largely teach the operators. And mass manufacturing operations will exist alongside all of this.
Can we expect these trends to be visible at the forthcoming Texprocess exhibition which you are jointly organising with Messe Frankfurt in May?
ES: Very definitely. One rapidly rising sector that of digital printing, where technical progress is making new solutions possible for the direct printing of clothing, footwear and technical textiles. Prior to digital printing, it was only possible to print textiles, but now we’re looking at finished garments. At Texprocess for example, we’ll see the emergence of technologies for the merging of the printing and cutting stages as a further development. The ‘Digital Textile Micro Factory’ will also be running throughout the show, to demonstrate the ease with which such new operations can now be rapidly established. There will be many other examples of smart new technologies on display in Frankfurt from May 9-12th.
Business intelligence for the fibre, textiles and apparel industries: technologies, innovations, markets, investments, trade policy, sourcing, strategy...
Find out more