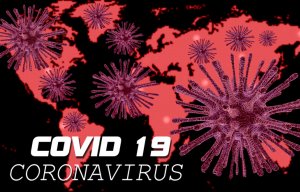
AATCC warns against false anti-viral product claims
Innovation in Textiles talks to Mark Shelton, managing director of UK-based Shelton Vision.
7th March 2023
Innovation in Textiles
|
Leicester, United Kingdom
Talking to Adrian Wilson, Mark Shelton outlines the untapped benefits of sharing data from accurate, reliable and consistent automated fabric inspection systems for textile manufacturers and their customers.
Innovation in Textiles (IiT): What are the chief benefits of the Shelton WebSpector?
Mark Shelton (MS): The most obvious is the potential to reduce the cost of labour associated with inspection by increasing throughput speeds to around ten times that of manual inspection. Today there is also a lack of available or willing labour to perform this mundane but previously essential task.
Apart from increased throughput there are other advantages that offer far greater return. Usually the largest of the quantifiable sources is that of optimising the sales value on goods that are produced by minimising waste and eliminating claims.
The calculation for revenue value optimisation involves converting a proportion of ‘waste’ back to first quality product and adding back the gain in revenue to the bottom line.
This is achieved by applying an optimised cut plan calculation, with the required cutting rule sets, to the defect map generated by the vision system for a batch prior to cutting into small rolls. The result is an optimised cut plan in virtual form where the final first quality yield result is known prior to physical cutting.
In some cases, there will be the opportunity to significantly further improve the yield of a batch by editing the map, or by having more flexible optimisation rules (such as increasing the roll length tolerance). The great significance of running the optimisation on an electronic or ‘virtual’ map, is the certainty of the outcome of the cutting process before the batch is cut. In addition to being viewed in the manufacturing plant, this process can be viewed remotely and decisions made remotely by companies with offshore or multiple manufacturing plants.
IiT: How can the output data from such systems assist the processes of a mill’s customer?
MS: With the power of visual records retained in the Shelton WebSpector system, fabric producers have more information about their products than their customers, even when the fabric has been shipped.
With a WebSpector system the fabric producer can now provide its customers with additional early information, in advance of shipping, directly from its inspection process adding significantly to both efficiency along the value chain and waste reduction.
There are opportunities to work more closely with the customer who can, for example, be emailed an inspection report the instant the product leaves the final process in order to sign off a batch – even before it enters the mill’s warehouse. This provides the reassurance of knowing the customer’s production (or retailer sales window) will not be disrupted by unknown quality issues, late shipments or short shipments. It can serve to attract more business from existing customers and/or attract new customers who would rather place business with an organisation that has this degree of control. Additionally, if the customer has compatible lay planning and production optimising software, the electronic defect map can be easily incorporated into the software to optimise cloth utilisation in the panel cutting process.
The consistency of the system’s performance means both parties can be sure the inspection has been performed to the agreed level and the settings can also be audited. It is therefore less likely that claims will be made and more importantly, the reasons for claims are removed, as are the costs of resolving them. Such costs include increased lead times, lost production, planning logistics, airfreight, re-processing, value added compensation etc.
Once a mill’s customer understands the level of control the mill has with its inspection system, it will be happy to avoid duplication of the inspection process.
IiT: Can the benefits extend throughout the whole value chain?
MS: In the garment manufacturing sector it is increasingly important to ensure fabric deliveries are made in full and on time to enable the garment maker to meet retailer delivery requirements. This is critical as production runs are shrinking and there are shorter ‘seasons’ in most retail businesses. By eliminating inspection duplication, shipping unknown defects in cloth and providing data to optimise the lay planning and cutting process prior to receipt of the physical fabric, there is a vast opportunity to reduce lead times, avoid cost/process looping, eliminate claim disputes and streamline the whole garment value chain.
IiT: How does the inspection system accommodate multiple styles and performance validation?
MS: In most textile inspection applications there are often several hundreds or thousands of unique styles running over the period of a year. The challenge of detecting real defects and not reporting ‘non defect’ features requires fundamental capabilities of automated style training by the system and a powerful performance validation tool.
In order to provide the optimum inspection settings for a large and ever changing range of styles or products, the Shelton WebSpector has an automated style training feature (WebTRAINER) which enables it to train itself on each unique style or product and then store the settings and continue to inspect. This means that there are no ‘default setting’ compromises in the detection settings and ensures that thousands of different styles can be handled at optimum performance without operator intervention as and when new styles are introduced.
To avoid over and under detection as seen in basic vision systems, the WebSpector system is specified from our experience and evaluation of a set of typical borderline defects provided by our clients. During commissioning our engineer will use the virtual roll recording feature (WebCORDER) to store video of work orders as they are trained on and inspected by the system. These stored videos of the workorders are then used to carefully compare the system generated defect maps to the results of a critical manual inspection.
Small adjustments to the settings can be made at this stage until the output of the inspection system meets the required level. The benefit of the recording feature is that everyone can see how well the system is performing and the video can be run as often as required to validate the results without having to physically re-run the fabric. This is particularly useful where the inspection is done in process, or at the end of a process, where the fabric cannot be physically re-run to test the changes made.
Business intelligence for the fibre, textiles and apparel industries: technologies, innovations, markets, investments, trade policy, sourcing, strategy...
Find out more