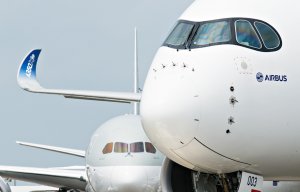
Teledyne CML Composites awarded A350 Airbus contract
When the Airbus A350 XWB takes to the skies for the first time this summer it will be a momentous achievement for Airbus and one of the proudest moments in Hexcel’s 65 year history – especially as every A350 XWB that takes to the skies generates over $4 million in sales for the US composites manufacturer.
25th March 2013
Innovation in Textiles
|
Paris
When the Airbus A350 XWB takes to the skies for the first time this summer it will be a momentous achievement for Airbus and one of the proudest moments in Hexcel’s 65 year history – especially as every A350 XWB that takes to the skies generates over $4 million in sales for the US composites manufacturer.
The A350 XWB is the first Airbus with a structure that is over 50% composites – 53% in fact, whereas composite materials constituted only 15% of the structure of the A340 and 23% of the A380. The A350 XWB lower wing covers are the largest single civil aviation parts made from carbon fibre, measuring 32 metres long and 6 metres wide.
When Hexcel was awarded the contract in 2008 to supply carbon fibre prepreg for all the A350 XWB composite primary structures, it was the largest contract in the company’s history, expected to generate revenues of $4-5 billion. By February this year Airbus had sold 617 A350 XWBs.
Hexcel secured the A350 XWB contract by developing a complete composite proposal including carbon fibre prepreg and associated products. The company’s experience in Intermediate Modulus carbon fibres was used to design HexTow IMA to Airbus requirements and HexPly M21E prepreg resin matrix was developed by Hexcel chemists to ensure that the very high performance properties in the fibre are fully optimized in the cured prepreg laminates.
The A350 XWB composite structures built by Airbus and the Tier 1 suppliers using HexPly M21E/IMA include entire fuselage panels, keel beam, the entire wing (covers, spars and centre wing-box) and empennage (tail assembly).
To meet the increasing demand for HexTow carbon fibre, new lines have been added at Hexcel’s PAN precursor facility in Decatur, AL; new carbon fibre lines have been commissioned in Salt Lake City, UT; and Hexcel has built its first European carbon fibre manufacturing plant in Illescas, Spain.
To produce the vast quantities of prepreg required for the A350 XWB Hexcel introduced a new model for the cost-effective large scale production of prepreg, producing resin film in a continuous process to very tight aerial weight tolerances in Duxford, UK, which it says has improved the quality, accuracy and consistency of the resin film. Hexcel is also expanding its prepreg matrix capacities at its Salt Lake City, Utah facility.
The resin film from the UK is converted into UD prepreg at Hexcel facilities in France, Spain, Germany and the USA from where it is supplied to nearby Airbus facilities and the Tier 1s throughout Europe and the USA.
This has resulted in a highly effective supply chain model for prepreg production, which benefits the customer and Hexcel, resulting in shorter lead times, greater responsiveness, reduced transportation of materials, point of use delivery, less packaging, reduced inventory and fewer requirements for cold storage space.
“We are very much looking forward to celebrating the A350 XWB first flight later this year” said Nick Stanage, Hexcel President and COO.
“Since we were awarded the contract by Airbus back in 2008 we have delivered on our commitments by investing in Hexcel’s global capacity as required for the A350 and other aircraft programs. Our expansion has been successful because of our close cooperation with Airbus and their global partners. The combination of advanced technology and operational excellence is the foundation for our business at Hexcel and I wish to thank our Hexcel team, suppliers and valued customers who are working on the A350 program for their dedication and commitment.”
The following videos give a really good insight into the processes used by Hexcel's customer Airbus in the manufacture of the A359 XWB:
In this video clip, team members at Airbus’ Broughton, UK site discuss the facility’s contribution to A350 XWB production – which focuses on wing deliverables.
The contributions of Airbus’ Stade site to production of the next-generation A350 XWB jetliner are highlighted in this video clip, with comments from a number of Airbus team members.
Hexcel is a global leader in advanced composite materials for aerospace and wind energy markets, as well as some selected industrial applications. A technology trailblazer, Hexcel develops, manufactures and sells a very wide range of composite materials and processes for selected markets, from carbon fibre to reinforcements, adhesives, honeycomb, prepregs, engineered core and engineered products.
The company achieved $1.6 billion in sales in 2012 and forecast solid growth, based in particular on successes on new commercial aircraft programs such as the A350 XWB. Hexcel is predicting double digit growth over the next 5 years and anticipates achieving sales of around $2.5 billion by 2017.
With a workforce approaching 5000, Hexcel has 18 manufacturing sites, located throughout the USA, Europe and Asia.
Business intelligence for the fibre, textiles and apparel industries: technologies, innovations, markets, investments, trade policy, sourcing, strategy...
Find out more