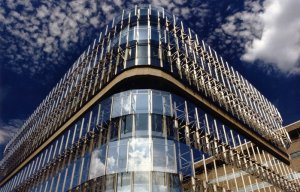
Fashion for Good launches new partnership
Rotating spinneret is sectioned into three sub-disks.
21st May 2021
Innovation in Textiles
|
Daejeon, South Korea
A new nanofibre production technique developed at the Korea Advanced Institute of Science and Technology (KAIST) is said to achieve up to 300 times the output of the conventional electrospinning process.
Electrospinning has been the common process used to prepare fine and uniform polymer nanofibres but has several drawbacks, such as the requirement of a high-voltage electrical field and an electrically conductive target.
Existing centrifugal spinning technology employs centrifugal force instead of high voltage to produce polymer nanofibres and is being proposed as a safer and more cost-effective alternative to electrospinning. Achieving scale is another advantage, since the technology only requires a rotating spinneret and a collector.
However, because current centrifugal force-based spinning technology employs only a single rotating spinneret, productivity is limited and not much higher than that of some advanced electrospinning technologies such as multi-nozzle electrospinning and nozzleless electrospinning. This problem persists even when the size of the spinneret is increased.
In response, a research team led by Professor Do Hyun Kim from the Department of Chemical and Biomolecular Engineering at KAIST has developed a centrifugal multispinning for mass production, by sectioning a rotating spinneret into three sub-disks. The team’s findings have been published in ACS Macro Letters.
Using this new centrifugal multispinning spinneret with three sub-disks, the researchers demonstrated the gram-scale production of various polymer nanofibres with a maximum production rate of up to 25g per hour, which is approximately 300 times higher than that of a single spinneret in a conventional electrospinning system. The production rate of up to 25g of polymer nanofibres per hour corresponds to the production rate of about 30 face mask filters per day in a lab-scale manufacturing system.
By integrating the mass-produced polymer nanofibres into the form of a mask filter, the researchers were able to fabricate face masks that have comparable filtration performance with the KF80 and KF94 face masks that are currently available in the Korean market. The KF80 and KF94 masks have been approved by the Ministry of Food and Drug Safety of Korea to filter out at least 80% and 94% of harmful particles respectively.
“When our system is scaled up from lab-scale to an industrial unit, the large-scale production of centrifugal multispun polymer nanofibres will be made possible, and the cost of polymer nanofibre-based face mask filters will also be lowered dramatically,” Kim said.
Business intelligence for the fibre, textiles and apparel industries: technologies, innovations, markets, investments, trade policy, sourcing, strategy...
Find out more