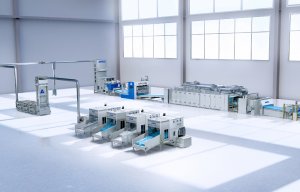
Comprehensive showcase for Andritz technologies
Computational fluid dynamics and software analysis employed to enhance air and fibre throughput.
19th February 2024
Innovation in Textiles
|
Europe
As part of an ongoing collaboration, the Fraunhofer Institute for Industrial Mathematics ITWM in Germany and Swiss engineering firm Siriotek have completed feasibility investigations on the latest AioLos airlaying machine being developed by Italy’s Bematic.
With airlaying technology, the raw material is opened and fed into an air stream using a roller and the air-fibre mixture is deposited on a belt using suction and then compacted before being bonded.
The study focused on simulating fibre dynamics inside the airlay machine to provide insights and data useful for optimising productivity and efficiency.
A detailed model using CFD (computational fluid dynamics) was developed by Siriotek engineers which includes moving boundaries to simulate the rotation of the main carding drum as well as the linear motion of the porous belts designed to promote web formation and the transport of the fabrics.
Results from the CFD analysis were then passed to Fraunhofer ITWM for use with its proprietary software FIDYST (FIberDYnamics simulation tool). Using material data, density and size for polyester fibres the Fraunhofer scientists were able to predict the motion of the fibres inside the airlay forming vane under the effect of turbulent airflow, effectively simulating the deposition process on porous moving belts.
The feasibility study also included further investigations covering process speeds as well as optimal design for the carding wire to be installed on the main drum and worker/stripper rollers operating upstream of the airlay aerodynamic vane.
Due to the encouraging results, Bematic has now committed fully to the new design and will manufacture a a full scale unit, with procurement of parts currently in progress.
“The collaboration with ITWM and Bematic has showcased the benefits of a joint technical/scientific approach to optimise airlay production processes for nonwovens,” said Giovanni Di Lorenzo, founder and chief engineer at Siriotek: “We are delighted that Bematic has now committed to the new airlay concept.”
“The feasibility study for the new airlay concept has been successful and Bematic is ready to venture into manufacturing and assembly of a full scale unit,” added Giovanni Bettarini, partner and commercial director at Bematic. “We look forward to delivering significant improvements in productivity and efficiency in nonwovens processing to our clients.”
Business intelligence for the fibre, textiles and apparel industries: technologies, innovations, markets, investments, trade policy, sourcing, strategy...
Find out more