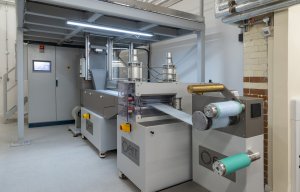
FET at INDEX 23
FET has already supplied one of these new spunbond lines to University of Leeds in the UK.
27th September 2021
Innovation in Textiles
|
Leeds, United Kingdom
The UK’s Fibre Extrusion Technology (FET) will introduce its new lab-scale spunbond system at the forthcoming INDEX 2020 nonwovens exhibition taking place in Geneva, Switzerland, from October 19-22.
Complementing the company’s successful meltblown technology, the new spunbond range provides unprecedented opportunities for the scaled development of new nonwoven fabrics based on a wide range of fibres and polymers, including bicomponents.
The market availability of this new technology is particularly timely, given the industry’s current preoccupation with the development of new substrates based on biopolymers, sustainable resins or recycled fibres.
FET has already supplied one of these new spunbond lines to University of Leeds in the UK, and a second, in combination with a metlblown line, to the University of Erlangen-Nuremberg in Germany.
“Our new spunbond technology is unique in providing the ability to process a wide range of polymers, including those normally not considered appropriate for the spunbond process, at the scale required to fully explore material combinations and bring new products to market,” says FET Managing Director Richard Slack. “FET has built on its melt spinning expertise to develop a true laboratory scale spunbond system.”
Properties
Steve Russell, Professor of Textile Materials and Technology at University of Leeds, agrees.
“Our new spunbond line from FET forms part of a wider investment in facilities to support fundamental, academic research on future manufacturing, where the focus is on studying the small-scale processing of unconventional polymers and additive mixes to form spunbond fabrics with multifunctional properties,” he says. “Key to this research is developing the underlying process-structure-performance relationships, based on the measured data, to provide a detailed understanding of how final fabric performance can be controlled during processing.”
Many exciting materials developed in academic research struggle to progress beyond the bench as a result of compatibility issues with key manufacturing processes such as spunbond, he adds.
“By leveraging mono, core-sheath and island-in-the-sea bicomponent technology, the Leeds team is working with polymer and biomaterial research scientists, engineers and clinicians to explore the incorporation of unusual materials in spunbond fabrics, potentially widening applications,” Russell says. “The new spunbond system is perfectly suited to our academic research work, and is already proving itself to be extremely versatile and intuitive to use.”
“We look forward to discussing the possibilities of this versatile new system with interested parties at INDEX in Geneva,” Richard Slack concludes. “It is capable of processing pure polymer with no requirement for processing aids or additives, to obtain a wide range of structural and mechanical properties, and there are numerous options for the post-processing of the webs.”
FET is at stand 1163 at the show in Geneva.
Business intelligence for the fibre, textiles and apparel industries: technologies, innovations, markets, investments, trade policy, sourcing, strategy...
Find out more