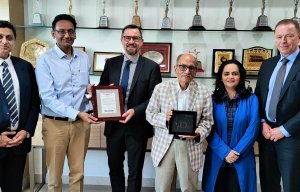
Trützschler honours the 100 Club
All machine orders from the last few months are now being installed.
31st March 2025
Innovation in Textiles
|
Moenchengladbach
Since it was launched in January 2024, Trützschler’s TC 30i generation carding machine has proven the top quality and higher productivity it can enable in the processing of both manmade fibre and cotton.
As a result of its intelligent, self-optimising functions, the TC 30i achieves consistent results from any raw material while reducing or eliminating the demand for operator intervention. The machine has already proven up to 40% higher productivity in manmade fibre applications and in recent trials with cotton applications, customers in Indonesia and Türkiye have also achieved outstanding results.
Mem Tekstil
In Türkiye, for example, Mem Tekstil is one of the largest integrated manufacturers in the textile sector with operations integrating ring, OE and Vortex spinning, knitting, dyeing and digital printing. With Trützschler’s TC 30i it has produced an Ne 20 yarn made from 100% cotton soft waste via OE spinning. Its engineers tested the TC 30i because they are considering upgrading older card models from a Swiss competitor. The TC 30i, however, has increased productivity from 70 kilograms per hour to 160 kilograms per hour with the same or better quality.
Safteks
Safteks is another Turkish Trützschler customer which produces cotton yarns with a monthly production capacity of 2,100 tons. It uses OE spinning to manufacture 100% Ne 20 cotton yarns from 40% virgin cotton and 60% cotton soft waste. Adopting TC 30i cards made it possible for Safteks to increase its output capacity from 70 tons per day to 85 tons per day – a productivity boost of more than 20%, with the same level of quality.
Budi Texindo Prakarsa
Budi Texindo Prakarsa is a leading spinning mill based in Indonesia, specialised in the production of premium cotton yarn, with an annual capacity of 80,000 spindles. In recent trials with the TC 30i, the company produced 100% cotton yarns in counts of Ne 20 to Ne 30 via ring-combed processes. Compared to the previous benchmark, productivity increased by up to 30% with the same quality level. At the same time, energy and air consumption per kilogram have been reduced.
New features
These success stories in carding cotton with the TC 30i are being achieved because the T-GO automated gap optimiser improves quality by enabling the smallest and most precise carding gaps – far beyond anything possible with manual settings. Secondly, the TC 30i maximises quality and productivity by increasing the number of active flats without sacrificing flexibility in the pre- and post-carding areas due to the larger cylinder diameter. Thirdly, the TC 30i minimises cotton waste as a result of a new and highly precise mote knife at the first licker-in. Customers can automatically optimise and adjust the mote knife settings to meet their specific needs. Combined with the impact of the Wastecontrol feature, this significantly reduces material waste.
PT Dhanar Mas
Also in Indonesia, PT Dhanar Mas Concern (Danar Mas) specialises in spinning yarns and manufacturing greige fabrics and is using a TC 30Si card specially customised for manmade fibres. In recent trials, Danar Mas has produced ring carded polyester yarns (Ne 20 to Ne 30) and a viscose yarns (Ne 30 to Ne 40) Via vortex spinning. In both applications, the card produced 125 kg/h of material – up to 40% more than the company produces with its current benchmark.
The next-generation TC 30i is suitable for a broad range of applications including fine count (with the TC 30Fi model) and recycling (with the TC 30Ri model). All orders from the last few months are now being installed and the TC 30i will soon be demonstrating its positive impact on productivity and quality at many more mills worldwide.
Business intelligence for the fibre, textiles and apparel industries: technologies, innovations, markets, investments, trade policy, sourcing, strategy...
Find out more