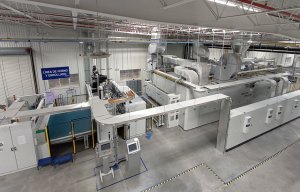
Brückner to present its full programme in Geneva
The new Supra-Flow BA is designed to guarantee a particularly gentle transport of the unbonded web.
21st March 2019
Innovation in Textiles
|
Leonberg
Brückner Supra-Flow BA. © Brückner
Brückner, a leader in production of finishing lines for the textile industry, will be presenting its new Brückner Supra-Flow BA air-through thermofusion oven at the upcoming Techtextil trade fair that takes place from 14-17 May in Frankfurt.
“Particularly in the field of hygiene nonwovens, the trend goes towards products of a better quality with a smoother handle, more volume and of more uniform texture. Nonwovens producers worldwide are supported by the new Brückner Supra-Flow BA belt oven, which gives them the technology to produce such high-quality end products.”
The new Supra-Flow BA is designed to guarantee a particularly gentle transport of the unbonded web. This is achieved by a sophisticated air circulation design. It is also said to be characterised by minimum heat consumption, high flow uniformity and constant temperature distribution over the entire working width. The dryer is available in working widths up to 4600 mm. It is designed for production speeds of up to 250 m/min and thus offers potential for line optimisation.
Brückner Supra-Flow BX. © Brückner
Typical end products, which are bonded on the Brückner Supra-Flow BA high-end thermofusion oven according to the air-through principle, are nonwovens for diapers (ADL, topsheet, backsheet), nonwovens for feminine care and incontinence products but also filter nonwovens and special nonwovens.
One year ago, Brückner presented the revised double belt oven for thermofusion of high-loft nonwovens to the expert public. The aim was to reduce the use of primary energy with a view to resource-conserving nonwovens production and thus to reduce production costs. With the double belt furnace Supra-Flow BX, Brückner’s engineers succeeded in achieving not only this increase in efficiency, but also the re-construction of the air circulation with fewer individual parts. There were also many small detail improvements, and in 2018 many Supra-Flow BX were sold in different configurations.
The oven is suitable for the production of high-loft nonwovens, medium as well as highly com-pressed fibre boards made of natural, synthetic and/or recycled fibres. It is a convective oven system, which works according to the air-through principle. In each compartment the flow direction can be individually adjusted according to the product requirement. In most cases the basic material beside the matrix fibres are binding fibres melting at low temperatures such as bi-component fibres (PES/CoPES, PP/PR) and PP. Thermoplastic or duroplastic powders can be used also as binders.
Brückner Supra-Flow BE. © Brückner
The Supra-Flow BX is particularly suitable for products with a higher weight, thickness and/or density and relatively high-pressure losses during the flow through the product.
This type of oven is particularly suitable for the gentle drying of binder-bonded lightweight nonwovens. For such lines Brückner can supply the belt dryer type Supra-Flow BE, as well as the foam padder, the cylinder dryer group and a smoothing calender downstream of the dryer. The Brückner Supra-Flow BE is successfully in operation and produces high-quality nonwovens for the medical sector, the company reports.
Brückner has again improved its minimum application unit. The customer has the following advantages over a padder: Low-Add-On technology, low water consumption, high energy savings in the subsequent drying processes, low residual liquor, and thus fewer chemicals which have to be disposed of during a batch change.
The Eco-Coat unit enables impregnation and precise one-sided Kiss Roll coating on the upper or lower side of the fabric web as well as functionalisation such as hydrophobisation or softener application by means of engraving roller pre-dosing. In addition, one-sided ink jet preparation is possible. Single-sided functionalisations with a wide variety of finishing chemicals can be realised, especially for fashion and technical applications.
Business intelligence for the fibre, textiles and apparel industries: technologies, innovations, markets, investments, trade policy, sourcing, strategy...
Find out more