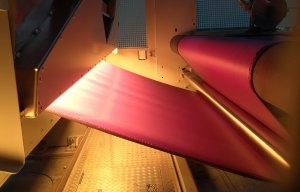
Tintex uses Brückner line to coat novel knitted fabrics
Portuguese textiles company Tintex Textiles and German textile machinery manufacturer Brückner Textile Technologies are taking a big step into the future together.
15th January 2021
Innovation in Textiles
|
Villa Nova, Portugal
The Portuguese textile company Tintex Textiles S.A. and the German textile machinery manufacturer Brückner Textile Technologies GmbH & Co. KG are taking a big step into the future together with a newly developed process technology for coating bi-elastic knitted fabrics. The new development will open new markets and new possibilities for both sides.
Tintex, a modern textile company located in Villa Nova, not far from the Spanish border in northern Portugal, was founded in 1998 in the region of Porto. Tintex’ product range includes functional tricot fabrics for well-known fashion, sports and lingerie brands. The company is convinced that fashion can truly make a difference in tackling climate change. That is why its engineers are constantly developing new strategies and environmentally friendly concepts throughout the whole production process. Tintex’ technologists' expertise covers the entire textiles supply chain, including dyeing and finishing techniques as well as coatings.
No sustainability without innovation
True to the motto, ‘no sustainability without innovation’, Tintex is constantly researching new fabric innovations to develop and produce intelligent, functional and high-performance textiles and to round off the concept, a few years ago it decided to cooperate with the German textile machinery manufacturer Brückner.
The goal is always to think and act with long-term perspective, because this is the only way Brückner and its customers can be successful in the long run
Brückner’s product range includes machines and complete lines for coating and finishing of textiles, technical textiles, nonwovens and floor coverings. With its own production site in the south of Germany, completely re-built in 2018, Brückner has become even more flexible and competitive. The family-run company was founded in 1949 and is today managed by second generation Regina Brückner and her husband Axel Pieper. Still valid today, the values and visions of the company’s founder are the key to success: the production of high-quality lines, the development of sustainable and innovative technologies and the competent and comprehensive advice of its customers.
Since both companies, Tintex and Brückner, share the same philosophy, the basis for constructive and goal-oriented product development was quickly established. Tintex’ vision was to be able to achieve completely new effects on bi-elastic knitted fabrics and to produce fabrics that did not even exist before. This was followed by numerous tests in the Technology Centre at Brückner in Leonberg and on a Brückner line in an institute for textile and process engineering near Stuttgart.
According to Brückner, a new, revolutionary line concept was worked out together, which has unbeatable benefits especially with regard to the requirements of temperature uniformity, the thermal treatment of synthetic fibre blends and other constructive issues. Even very difficult knitted fabric with high elastane content can now be directly coated or functionalized. Until now, such coatings were only possible via an indirect coating process, the company says.
The heart of the new line is the proven, but constantly further developed and optimized Power-Frame stenter frame dryer. The inlet and outlet components are specially designed for sensitive fabric and ensure tensionless fabric run. A special, newly developed coating unit is integrated in the infeed stand of the stenter frame. Due to its variable design, two different application processes are possible on the same line. In the so-called screen coating process, water-based pastes and stable or unstable foams are applied onto the fabric with high precision by means of a driven, cylindrical screen and a squeegee system integrated in the screen.
For paste coating, the machine parameters can be adjusted in such a way that a single-side coating is possible even on light knit goods made from cotton or viscose, provided the paste is of a suitable viscosity. For the stable foam coating, the coating medium is mixed to foam with an exact foam/litre weight of 150 to 300 g/l. With an integrated feed pump, this foam can be precisely dosed and applied to the textile through the screen. Also, in the case of unstable foam coating, the coating medium is foamed up with a mixer and applied to the textile in exact doses. Here the foam/litre weight is 30 to 100 g/l.
As the unstable foam collapses shortly after leaving the screen, a single-side functionalization with a very low pick-up of less than 10-20 % can be achieved. This is a minimum application with the corresponding benefits, e.g. considerable energy and thus cost savings in the subsequent drying process. If you want to coat somewhat more stable fabric or apply higher coating weights, the unit can be quickly and easily converted from screen coating to a knife-over-cylinder system. The counter pressure roller is then used as coating cylinder.
A laminating/embossing calender integrated in the outfeed of the stenter allows various effects to be achieved on the fabric, e.g. a leather grain. If the applied stable foam coating has a certain layer thickness, this effect can be achieved after the drying passage in the laminating calender by means of a fed release paper or an appropriate embossing roller. Even with sensitive, directly coated knitted fabric, the calender can be used to apply, for example a film, a membrane or a second textile web onto the fabric. For this purpose, the calender is additionally equipped with an electric short-wave infrared dryer.
For simple heat-setting processes a special roller has been developed which can be inserted into the coating unit instead of the screen and thus acts as the upper infeed roller. Even very tension-sensitive knitted fabric can be run with an overfeed of up to 60 % before heat-setting.
The new multifunctional line can therefore be used for heat-setting, drying and coating processes. It can be used to manufacture products comparable to those previously produced with indirect coating - but without having to rely on cost-intensive release paper.
At Tintex in Portugal, production on this line has already been running for some time and research into completely new types of textiles is continuing. Tintex won the Hightex Award with such newly developed products at Munich Fabric Start, as well as the Innovation Award at Techtextil in Frankfurt.
Brückner says it is very proud to have customers like Tintex who act with foresight and do not strive for short-term profit optimization. The goal, the company says, is always to think and act with long-term perspective, because this is the only way Brückner and its customers can be successful in the long run.
Business intelligence for the fibre, textiles and apparel industries: technologies, innovations, markets, investments, trade policy, sourcing, strategy...
Find out more