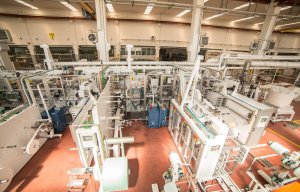
Two diaper lines for Nigeria
Highlighting technologies for recycling and the processing of natural fibres.
24th May 2022
Innovation in Textiles
|
Graz, Austria
A focus of Andritz at this year’s Techtextil in Frankfurt from June 21-24 will be on airlay and recycling technology as well as bast fibre processing technologies, following the company’s acquisition of Laroche, now renamed Andritz Laroche.
This includes complete recycling lines for post-consumer and industrial textile waste to produce fibres for re-spinning and/or nonwoven end-uses. Customer awareness and regulations are forcing clothing brands to recycle their textile waste in their own products, the company observes. Recycled fibres can also be used in the nonwovens industry for various applications, for example in the automotive industry for insulation and in mattresses and furniture felts.
Andritz Laroche offers a complete range of tearing lines capable of handling up to 3,000 kg/h, which can be used for almost all types of pre/post-consumer textile waste. The aim is to preserve the character of the original fibres such as cotton, by maximising fibre length, strength and feel.
The Exel and Jumbo Exel tearing machines are user-friendly and equipped with tailor-made automated solutions to remove the non-textile parts from post-consumer waste and unsold items. The Exel has a production capacity of 400 to 800 kg/h depending on the raw material.The Jumbo Exel has a higher production capacity of 600 to 1,200 kg/h depending on the raw material.
This technology enables complex industrial waste to be processed into fibres such as trunk liners, door trims, floor and dash pads and various needlepunched felts.
A team of experts assists Andritz customers in conducting customer-specific trials at the company’s technical centre in Cours, France.
Durable applications
The use of nonwovens in the automotive sector has increased dramatically in recent years and based on decades of experience, Andritz develops cost-efficient and reliable turnkey needlepunch and airlay lines.
The recent boom in the market for durable nonwoven products led Andritz to develop its PA3000 elliptical pre-cylinder to meet the demand for higher capacities and lighter products. It consists of an optimised pre-needleloom cylinder for the production of light webs and provides greater speed and width. The lack of friction between the web and the rolls provides a perfect appearance. In addition, the automotive industry is shifting its focus to sustainable technologies, and this is having a direct impact on the properties of nonwoven parts in vehicles.
The ProWin technology for profile weight correction in the needlepunch industry is used to optimise processes, provide a faster return on investment and save raw materials. The unit combines the well-known ProWid and ProDyn systems, enabling even better performance. ProWin minimises the level of instantaneous acceleration as well as the maximum internal speed. As a result, the same machine can run faster with less mechanical stress. Andritz will also be presenting its ProWin technology at the VDMA spotlight talk during Techtextil, to be held at 10:30 am on June 21 at the VDMA booth, and also be live-streamed.
Airlay
Airlay technology also plays a major role in durable nonwovens, for the automotive industry, building insulation, carpet underfelt, the mattress industry and furniture applications. This process includes blending, metering, opening, the airlay process and mat consolidation by needling, thermobonding, a combination of both, or spunlacing. Andritz offers three different types of airlay line – Airlay Flexiloft, Airlay Flexiloft+ and Airlay Resinfelt.
Airlay Flexiloft and Flexiloft+ have been designed to form mats from all types of fibres – from short and recycled to long and coarse – and from blends with non-fibrous components, such as plastic, foam or wood chips. Line widths range from 1.5 to 4 metres.
Airlay Resinfelt has been designed for thermoforming processes in the automotive and appliance industries. Manufacturers can offer weight ranges from 500 to 2,500 gsm over 2.4 metres in working width. Airlay Resinfelt retains the advantages of true air-forming technology and is especially designed to add resins to the mat, which is then semi-cured in a steam oven.
Wetlaid
Nonwoven end products based on glass fibres can be found almost everywhere – in ceiling tiles, cushion vinyl flooring, insulation, wallpaper and surface coverings, geotextiles, batteries, and, of course, roofing materials, as well as in many other applications. The market for glass-fibre mats is growing due to an increasing amount of construction and civil engineering work worldwide, as well as the great variety of applications for this material. The Andritz neXline wetlaid is a complete wetlaid production line for the production of glass mats. Different types of line are available depending on the capacity level. However, they all comprise stock preparation, wetlaid forming, binder application, a flat dryer and winder, and can perfectly matched to customer needs.
Business intelligence for the fibre, textiles and apparel industries: technologies, innovations, markets, investments, trade policy, sourcing, strategy...
Find out more