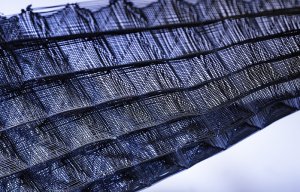
Monforts to debut its texCOAT coating range at Techtextil 2017
The exclusive wallcovering collections o are to be found in the very best guest rooms of the world’s finest hotels, in executive boardrooms and offices and in top-of-the-range luxury new housing developments
6th December 2016
Innovation in Textiles
|
Helmond, The Netherlands
The exclusive wallcovering collections of Tapetex, based in Helmond, The Netherlands, are to be found in the very best guest rooms of the world’s finest hotels, in executive boardrooms and offices and in top-of-the-range luxury new housing developments from Europe to the USA and to the Middle East and Asia.
The family-owned company, with a 50-strong workforce at the plant in Helmond, takes the finest fabrics of Europe’s most advanced weaving mills – pure silks, linens, jacquards, wools and suede – and turns them into unique collections via a combination of in-house design know-how and advanced finishing techniques.
“Our aim is to always come up with materials that other companies simply can’t make,” said Managing Director Bart van den Broek, whose father founded the company in 1975 as a trading operation, before deciding to bring full finishing processes in-house a decade later, in order to be completely in control of quality and the just-in-time distribution network.
“We opted from the start to concentrate solely on wallcoverings and our collections are now well known to architects and specifiers worldwide. Manufacturers for other markets attempt to enter the field quite often, but find it harder than they anticipated because it’s a complex market. They come and go.”
The Tapetex plant is equipped with all of the latest technology for laminating and embossing, dyeing, double-sided coating and heatsetting, crushing, flocking, laser engraving and digital and conventional printing, including a Monforts Thermex dyeing line for both wovens and nonwovens.
The company’s latest digital printing line is capable of simultaneously printing three different designs on 110 cm diameter jumbo rolls.
During 2016, a 2.2 metre wide, six chamber Monforts Montex 6500 stenter has been installed in a new 4,000 square metre expansion at the Helmond site.
“An older stenter is still being used for more limited runs,” said Mr Van den Broek, adding, “but with the new Montex line we can do much more. It has allowed us to introduce a number of new processes that were previously not possible.
“We can run coating and finishing processes that need better temperature, moisture, and air speed parameters in a much more controlled way,” he confirmed.
It is one of the most meticulously clean plants in the world, and in as an extra measure, all fabrics are brushed as an initial step in eliminating dust and potential contaminants prior the start of the finishing and converting steps.
“We need to be sure every metre of fabric is perfect from the first to the very last of a production run,” said Mr van den Broek. “It’s about reliability and repeatability.
“The Montex 6500 stenter has been running very well and gives us complete computerised control of all parameters such as temperature, moisture and setting times.
“We make all our own finishing chemicals and dyes in-house and try to do as much as possible ourselves. We deal with a lot of expensive woven materials and quality has to be guaranteed – especially if an order is being shipped to the other side of the world from here.
“With these kinds of fabrics, even the smallest of mistakes can be very expensive. There can be anywhere up to ten separate stages to the finishing of some of these fabrics, so we rely on the best computerised technology.”
The Tapetex collections are generally subtile and subdued, with an understated appearance often belying the sophisticated techniques behind their creation.
A material like Graphic Spirit, for example, is a tri-dimensional suede wallcovering which has intricate laser cut patterns revealing the nonwoven polyester base fabric and with silver and gold touches imprinted around its 3D crenulations.
Tech Inspirations, meanwhile, is a linen which has been cleverly embossed in variated grid lines, its design trialled on a lead template, so that its shimmers as the eye moves across it and the viewer moves across a room, while Crafty Deformation has a very fine 10% polyester warp thread running through its enhanced linen structure.
These are just three examples of the close to 400 fabrics in widths of 110 or 137cm rolls that Tapetex keeps in stock and currently sells to over 70 countries worldwide via its sales offices and agents.
“Our customers generally like to order at the very last minute that a job is specified and appreciate the ready availability of what they want, which can be shipped anywhere in the world in a matter of days,” said Mr van den Broek. “We have established a very good logistics network worldwide.”
Tapetex collections are designed and their processing routes perfected over a three-year period and made available for around the same time before being updated.
The company is currently putting together its latest range of wallcoverings based on both wetlaid and spunbonded nonwovens.
“Again, many of these products are supplied in several laminated layers with several coatings and usually double-calendered to provide the perfect finish we need,” Mr van den Broek concluded.
“Our nonwovens collections are not cheap, but the materials fall between the general market for vinyl wallcoverings and our high-end wovens. Their big advantage is that they allow the walls to breathe, and in some regions mildew is a big issue, so there’s no danger of that with these products.
“The walls on which are materials are eventually hung are essentially inspection boards. With other textiles in bigger production runs there are small mistakes that can be worked with, but in what we do there’s absolutely no margin for even the smallest error.
“The new Montex 6500 is helping us achieve this very high quality standard.”
Business intelligence for the fibre, textiles and apparel industries: technologies, innovations, markets, investments, trade policy, sourcing, strategy...
Find out more