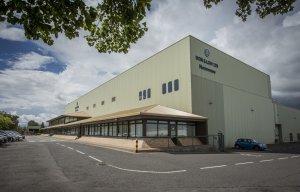
Don & Low expands UK capacity
Through its membership in Dörken Group, Multitexx benefits from almost two decades of spunbond production know-how.
13th March 2017
Innovation in Textiles
|
Heslington
Responding to the demand for lightweight, high-strength spunbond nonwovens, a new company Multitexx, based in Herdecke, Germany, is offering high-grade polyester (PET) and polypropylene (PP) spunbonds for challenging applications.
Through its membership in the internationally operating Dörken Group, Multitexx benefits from almost two decades of spunbond production know-how. The parent company, founded 125 years ago, was already developing and producing underlay sheets for pitched roofs as early as in the 1960s. In 2001, Dörken acquired a Reicofil spunbond line and began its own in-house production of spunbonds for the composite construction laminates market.
“After 15 years, the rapid growth of business made it necessary to procure a second, extremely high-performance Reicofil line,” the company explained. “This solved the production capacity problems at Dörken, and also triggered the establishment of Multitexx.” Since January 2015, the new company has been selling high-grade spunbonds made of thermo-calendered polyester or polypropylene.
The two Dörken Group's Reicofil lines can alternate between the two polymers and manufacture spunbonds of either material with low grammage and very high consistency. The polymers enter the production lines through separate feed lines that are modified for the respective raw material. Since polyester granulate agglutinates at a temperature of 80°C, it has to be pre-crystallised and dried before extrusion. It is then fed into the metering chamber which feeds the extruder. Polyester is extruded and melted at significantly higher temperatures than polypropylene. The melted polymers – PET or PP – then move on to the spin pump.
The melt is conveyed into the spinneret and distributed seamlessly over the full width of the line via a single-piece die. Thanks to its single-piece construction, which is configured to the production line's working width of 3.2 metres, the die prevents the potential flaws in the nonwoven that might form due to the welds created by multi-piece dies. In this way, the spinneret of the Reicofil line creates filaments with a filament count of around 2.5 dtex. These are then stretched into endless filaments through a long diffuser with temperature-controlled air and high air speeds.
The unique identifier of these spunbond products is the oval-shaped imprint created by the embossing roller in the thermo-calender. The rounded embossing is designed to improve the tear resistance of the nonwoven product. Subsequently the high-grade spunbond nonwoven goes through the stages of cooling line, defect inspection, longitudinal cutting, cross cut unit and winding before it finally arrives in dispatch.
Multitexx offers polyester spunbonds with a filament fineness of around 2.5 dtex, in a wide range of grammages from 15 to 150 g/m². In addition to high uniformity, their product qualities are also said to include high tear-strength, temperature resistance and very little shrinkage. In the case of polypropylene spunbonds, available grammages of nonwovens made of pure PP filaments range from 17 to 100 g/m².
The main customer for Multitexx spunbonds is the automotive industry. A range of spunbond variants are used in vehicle construction, for example as sound insulation, as electrical insulation or as material for filter elements. Their high degree of uniformity also makes them eminently suitable for the fluid filtration sector, where they are successfully deployed in a range of tasks from cooling lubricant filtration to beer filtration, the company reports.
Both spunbond lines are in round-the-clock operation – with a correspondingly high throughput. According to the company, GKD's CONDUCTIVE 7701 circulating laydown belt – 3.8 metres wide and almost 33 metres long – meets a wide range of standards making it suitable for withstanding the strain long-term. The belt structure is designed to facilitate good air permeability and the uniformity of the mesh. The easy cleaning properties of the GKD belt is also said to provide for the high production efficiency.
“In terms of its product features, the GKD belt is the best we've ever had on our production line,” said Andreas Falkowski, team leader of spunbond line 1. For this reason, another belt was ordered from GKD and is currently being produced. This time, the belt will be the novel CONDUCTIVE 7690, which is characterised by a significantly rougher belt structure in the running direction.
This construction is said to give the belt a special grip that aims to improve traction in the laydown zone and at the same time further optimise the belt's cleaning properties. "We haven't ever had problems with starting up after a belt change, but the rougher surface should make it even easier to remove droplets from the belt,” said Andreas Falkowski.
Business intelligence for the fibre, textiles and apparel industries: technologies, innovations, markets, investments, trade policy, sourcing, strategy...
Find out more