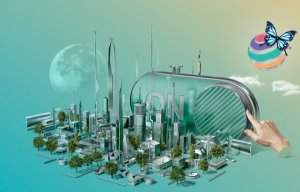
Groz-Beckert at ITME 2022
Dr. Anton Reinfelder (AR) is Managing Director of Groz-Beckert subsidiary Groz-Beckert Asia Private Limited, based in Chandigarh, India. He has corporate responsibility for the knitting and sewing divisions at two factories, local purchasing and also sales in India, Bangladesh and Nepal.
11th June 2012
Innovation in Textiles
|
Albstadt
Dr. Anton Reinfelder (AR) is Managing Director of Groz-Beckert subsidiary Groz-Beckert Asia Private Limited, based in Chandigarh, India. He has corporate responsibility for the knitting and sewing divisions at two factories, local purchasing and also sales in India, Bangladesh and Nepal.
In the following interview with Groz-Beckert (GB), Dr. Reinfelder gives an overview of the Indian textile markets, provides fascinating insights into national trends and developments and describes his expectations for this week’s ITMA ASIA + CITME exhibition in Shanghai.
GB: Dr. Reinfelder, Groz-Beckert has an excellent market position worldwide as a supplier of various different textile production and joining technologies. What is decisive as far as your markets are concerned?
AR: In Chandigarh, Groz-Beckert Asia (GBA) is known more familiarly as the "Needle Factory". We have a very good reputation in the town and the region and we're a preferred employer, known for treating our employees with fairness and respect. Our employees often retire after 30 or more years with the company.
In addition to the quality of our products, the textile industry really appreciates the expertise and service of our sales people, who have a high level of technical training. In India, people only do business with partners they trust.
After many years of business in India we've succeeded in gaining the trust of our partners and reinforcing it on a long-term basis. This has enabled not only to defend our market position in the knitting sector against partially cheaper competition, but also to successfully expand and develop our sewing sector as well.
GB: The Indian textile industry is one of the largest in the world. In 2011 it generated a total of roughly 55 billion USD. Fourteen percent of all textile fabrics and yarns are produced in India. Which sectors do you see as having the best growth opportunities in the future?
AR: Developments right now are being affected to a large extent by demand for constantly higher productivity. This is to combat rising wage costs but also to compensate for the fact that there just aren't enough qualified employees available. In addition to this, Western customers and an increasing number of Indian consumers are asking for textiles of high quality. In the light of this, I see three areas with growth potential:
Weaving – because of the technological shift from shuttle looms to looms without shuttles.
Textile processing – today it's considered a bottleneck. As part of a "forward integration strategy", costs and throughput times are being further reduced here. Plus, developments in textile processing could be a prerequisite for the production of, say, finer textiles.
Nonwovens – this relatively new technology is still at quite a low level in India today, but an increase in demand can be expected here. That applies to end-consumers as well as infrastructure projects.
GB: What's special about the Indian textile markets, in contrast to other textile markets in Asia?
AR: What makes India different in this regard is its higher flexibility. High-quality fashions and special designs are also produced in small batch sizes. And since English is spoken everywhere, even in small firms, this makes communication very efficient for foreign, primarily Western business partners.
GB: We have an important event coming up very soon for the entire textile industry, in the shape of the ITMA ASIA. What potential is the trade fair opening up specifically for GBA and for Groz-Beckert in India?
AR: In my view, the main emphasis at the ITMA ASIA will be on sales and procurement. Since the fair takes place only nine months after the ITMA Barcelona, presentation of new technologies will be the exception rather than the rule. There do seem to be some positive surprises in store, though – from Groz-Beckert, for instance, there's a new, innovative cleaning plant for weaving preparation.
Generally, we want to use the ITMA ASIA as an opportunity to position ourselves as a universal specialist for the most important aspects of the weaving process. The latest extensions where weaving machine components and weaving-preparation products are concerned are going to reinforce our position as a systems supplier for the weaving industry. Furthermore, we're expecting numerous existing and prospective customers from India who were unable to attend the ITMA in Barcelona.
GB: With the Technology and Development Center (TEZ), Groz-Beckert has created a unique platform for development work with its partners. How is the TEZ being received by Indian customers, and what kind of general feedback have you had?
AR: The feedback from major customers who have also been devoting some thought to the long-term development of their business is mainly positive. Some decision-makers from that customer group have already visited the TEZ and they're delighted with it. In one case, the visit put an end to discussions about our high price level and led to immediate needle orders.
The customer group from small and medium-sized enterprises are primarily geared toward optimizing the business costs from their existing production. Here the feedback has been a little more restrained. Which means that the challenge for our sales people here at GBA is to increasingly win over those companies to long-term partnership with Groz-Beckert.
GB: On the subject of Research and Development: The site at Chandigarh has its own sewing laboratory, where user problems are solved and new insights are gained into further development of the product portfolio. What are your experiences of the sewing lab thus far?
AR: The sewing laboratory began operations in 2002. Experience from over 900 projects and problem solutions has clearly confirmed there is demand for the lab. Customer value with regard to quality and cost reduction is high. In addition to pure problem-solving, we are getting an increasing number of queries before production starts at the customer.
In the laboratory we define the process parameters for a flawless and efficient production start-up. Close cooperation with machine and thread suppliers has also paid off in this "first time right" approach. GBA regularly organizes joint seminars on process design, and we've had good feedback here – in many cases also being able to recommend the use of our SAN10 needle.
GB: In Europe and North America, sustainable action is steadily developing into a cross-sector trend. What role does it play in Asia, especially where your regionally based company is concerned?
AR: Overall, the awareness that we have to protect our environment on a long-term basis has still not developed in a satisfactory way on the Indian subcontinent. Large companies have made sustainability an integral part of Corporate Social Responsibility (CSR) in their mission statements and are taking measures to save on energy or water, or to treat wastewater. And for some time now, companies intending to export to Europe or the US, for instance, have had to undergo a certification process with a focus on sustainable environmental protection.
In 2011 in Tirupur, one of the textile centres in Southern India, all the textile industry operations unable to prove that they had effective wastewater treatment in place were forced to close. This was the first radical step by the region's local government. Similar measures are expected in other parts of India as well.
At GBA, sustainability is a key component of our activities. We're happy to fulfill even stringent requirements, such as those relating to wastewater treatment. We've also introduced systems for tapping the wealth of solar energy in the region for heating water. All our employees go through an introductory program informing them of our mission and our actions where sustainability is concerned, and providing examples.
GB: The world's longest textile-reinforced-concrete bridge, in Albstadt-Lautlingen, Germany, is a landmark project where technical textiles are concerned. Groz-Beckert helped to realize this project. Are there any similar examples of this spectacular and highly effective material substitution in India?
AR: There are no spectacular examples in India just yet. The technical textile market is at a low level, compared with Western markets, of roughly 10 billion USD annually. High growth potential is evident, however – currently 11.25 percent per annum.
In its 12th five-year plan the Indian government is subsidizing the production of geotextiles, which is mainly concentrated in Northeastern India, with programs over 100 million USD. In the current fiscal year of 2012/2013, around one billion USD are planned as part of a venture capital program to support small and medium-sized enterprises.
A special focus here is the production of higher-quality textiles and also technical textiles. In addition to these programs, lower customs duties and tax breaks are aimed at facilitating investment in the technical textiles sector. By the year 2020 these measures could amount to a total market volume of around 37 billion USD.
GB: What particular risks and opportunities do you see for the Indian textile industry in the medium term?
AR: The biggest risk is the partly sluggish development of the infrastructure. Of course that applies to other branches of Indian industry, not only textiles. But the end result of it is that some textile centres have an insufficient power supply, and sometimes this leads to considerable production losses. I already mentioned that workers are becoming more expensive – that's another aspect.
In comparison with Vietnam, Cambodia or Bangladesh, this development could lead to India becoming a second choice. A lack of compliance on critical themes like environmental issues or child labour – especially in the case of small companies with no proper organization – is being projected onto the whole of the Indian textile industry and scaring off several Western customers.
Yet the opportunities outweigh the risks. The biggest potential for further growth in the Indian textile industry lies in the increasing buying power of the country's huge population, which also happens to have an unusually low average age of just 24.
Annual economic growth currently amounts to between 6 and 7%. As in other Asian countries that are steadily developing industrially, labour costs in India are becoming 10 to 15% more expensive each year.
This means risks but also opportunities, because in this way the development toward a higher-quality machine park with improved productivity is being accelerated. From conversations with our customers we've clearly noticed that this development is growing more rapid all the time. Overall, the Indian textile industry is getting better all the time at organizing itself.
One example here is the "forward integration" of spinning mills, which increases the amount of value-added in their own companies and significantly reduces overall throughput times. The integration process will drive demand for quality and productivity. In other words: Investments in new technologies will become necessary.
GB: Dr. Reinfelder, thank you for the interview – we wish you every success at the ITMA ASIA and all the best for the rest of the year!
Business intelligence for the fibre, textiles and apparel industries: technologies, innovations, markets, investments, trade policy, sourcing, strategy...
Find out more