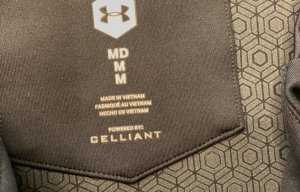
Bringing infrared wellness to more fabrics
According to a new report from Research and Markets, the global structure of polypropylene and polyethylene production is poised to change dramatically as capacity rises in China and soars in the Middle East. As a result, the shares of Western Europe and the USA are set to fall substantially, the report says.  The change in production structure will come about because the manufacture of propylene and ethylene-which are the main raw material feedstocks for pol
30th October 2009
Innovation in Textiles
|
Dublin
According to a new report from Research and Markets, the global structure of polypropylene and polyethylene production is poised to change dramatically as capacity rises in China and soars in the Middle East. As a result, the shares of Western Europe and the USA are set to fall substantially, the report says.
The change in production structure will come about because the manufacture of propylene and ethylene-which are the main raw material feedstocks for polypropylene and polyethylene polymer-is to start in the Middle East on a large scale. Also, large-scale production of the polymers themselves is about to begin.
Polypropylene and polyethylene fibres and filaments are used in a wide variety of technical textiles for agriculture, automotive, building and construction, hygiene, leisure, medical, outdoor and packaging applications. Specific end uses include active wear, artificial grass, bale wrapping, ballistic materials, bedding, carpet backing, car seating, diapers, disposable wipes, filter fabrics, fishing nets, flexible intermediate bulk containers (FIBCs), furniture, geotextiles, ropes and twines, sportswear, strapping, thermal underwear, upholstery and wall coverings.
Polypropylene and polyethylene filaments are normally produced by melt spinning. In this process, polymer granules-usually made by specialist producers rather than fibre companies-are fed to an extruder, which melts the polymer and then pumps it through a spinneret. Filaments are formed, and cooled in an air stream before being wound on a package or collected as a tow. In many cases coloured pigments are added to the polymer stream before extrusion because polypropylene and polyethylene fibres are difficult to dye.
Business intelligence for the fibre, textiles and apparel industries: technologies, innovations, markets, investments, trade policy, sourcing, strategy...
Find out more