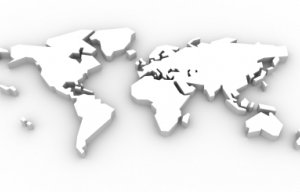
3B awarded Norway’s export prize for 2017
The collaboration was awarded through the US Department of Energy’s new High Performance Computing for Manufacturing programme.
13th June 2016
Innovation in Textiles
|
Pittsburgh, PA
PPG, a leading manufacturer of paints, coatings, optical products, specialty materials, glass and fibreglass, will partner with Lawrence Livermore National Laboratory (LLNL) to use high-performance computers to help reduce glass fibre breakage during the fibreglass manufacturing process.
The PPG/LLNL collaboration was recently awarded through the US Department of Energy’s new High Performance Computing for Manufacturing (HPC4Mfg) programme.
Fibreglass is made using a continuous high-speed process. If even one of several thousand glass fibres breaks while being pulled through a die (or bushing), it causes the entire bundle of fibres to break, wasting a significant amount of glass and energy until the manufacturing process can be restarted.
To help eliminate this waste, PPG and LLNL will develop numeric computer models to simulate the impact of thermal and physical environments on the glass-fibre forming process over a 4,000-tip bushing. The complexity and magnitude of the simulations requires the vast supercomputing resources at LLNL to model the process.
John Meng, PPG senior research associate, fibreglass, and principal investigator for the project, said the programme will develop models that, for the first time, are representative of real-world fibreglass manufacturing.
“The fibreglass industry has simulated the impact of varying one process parameter over many fibres and changing several process parameters over one fibre, but no one has modelled multiple process parameters over the thousands of fibres needed to adequately simulate actual production,” he said.
“The supercomputing capabilities at LLNL and PPG’s manufacturing expertise will enable us to develop sophisticated models that encompass all of these parameters. Ultimately, that will help us gain insight into fibre-forming and fibre-to-fibre interaction so that we can reduce fibre breaks through improved bushing design and fibre-forming processes.”
PPG estimates that continuous-strand fibreglass manufacturers in the US could save 1.7 TBtu annually by controlling fibre breaks. The company will provide US$ 99,000 in technical support to the project. The DOE will contribute US$ 300,000 to LLNL to fund its effort on the project.
PPG is one of several industry partners selected for award under the new HPC4Mfg programme. The Office of Energy Efficiency and Renewable Energy’s (EERE) Advanced Manufacturing Office (AMO) administers federal support of the HPC4Mfg program at LLNL.
AMO supports applied research, development and demonstration of new materials and processes for energy efficiency in manufacturing as well as platform technologies for the manufacturing of clean energy products.
Business intelligence for the fibre, textiles and apparel industries: technologies, innovations, markets, investments, trade policy, sourcing, strategy...
Find out more