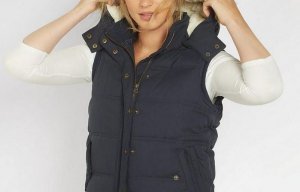
PrimaLoft to build on fashion success at Première Vision
The company makes advances toward goal of incorporating at least 50% recycled content in 90% of products by 2020.
13th June 2018
Innovation in Textiles
|
Latham, NY
PrimaLoft, a leader in providing comfort solutions with high-performance insulations, has taken the next milestone in its commitment to produce sustainable products by introducing its first three insulations made entirely from post-consumer recycled (PCR) material. They are produced through a proprietary process in which recycled plastic bottle chips are reconstructed into the form of high-performance fibres for premium insulation.
“Relentlessly Responsible represents our continuous commitment to providing sustainable solutions throughout our business in order to lessen our impact on the earth,” commented Jochen Lagemann, Managing Director Europe & Asia of PrimaLoft.
“We are striking an ideal balance between performance and sustainability, advancing our products without sacrificing either characteristic. PrimaLoft 100% PCR insulations deliver the best-in-class performance attributes that have made PrimaLoft a leader in performance comfort. These advanced technologies build upon the wide variety of choices we offer our brand partners and retailers who are looking to incorporate sustainable materials into their ranges.”
To date, PrimaLoft has saved more than 84.7 million plastic bottles from landfills and transformed them into premium insulation technologies, according to the company. By 2020, the company aims to make 90% of PrimaLoft insulation products with at least 50% PCR content.
Beside the new 100% recycled products, PCR content has been introduced to many popular PrimaLoft products, especially in the outdoor industry: products like PrimaLoft Gold Insulation and PrimaLoft Gold Insulation Active+ each currently contain 55% PCR fibres. PrimaLoft Silver Insulation Active is comprised of 65% of recycled material.
When PrimaLoft set out to increase its focus on delivering sustainable products, the company committed to introducing post-consumer recycled content without compromising performance or increasing price. “Advancements in the supply chain and PrimaLoft capabilities are crucial in this effort,” the company explains. “This way the PrimaLoft R&D-team was able to create recycled material that meets the same high-performance standards such as a warmth-to-weight ratio or lightness and packability.”
“The process of recycling sounds quite simple: Plastic bottles are collected, and the bottles are cleaned and shredded into chips. Those chips are again crushed into smaller plastic pellets and melted down. In a very special process PrimaLoft then creates high-performance PrimaLoft fibres, which in the end become various PrimaLoft insulation products, with all the performance attributes that both brands and consumers have come to trust.”
PrimaLoft is dedicated to reducing its impact at all levels of the business, from development through to manufacturing, focusing on energy and carbon emission reduction. Moreover, PrimaLoft striving towards developing natural plant-based fibres. First successful projects have already been realised together with Vaude by using Kapok fibres in a joint insulation development.
PrimaLoft works closely with highly recognised partners in this mission. For example, PrimaLoft is the world's largest manufacturer of bluesign-certified insulation materials with 90% of its complete product line receiving certification. All PrimaLoft products also comply with the Oeko-Tex Standard 100. The company is also part of the Sustainable Apparel Coalition (SAC).
Business intelligence for the fibre, textiles and apparel industries: technologies, innovations, markets, investments, trade policy, sourcing, strategy...
Find out more