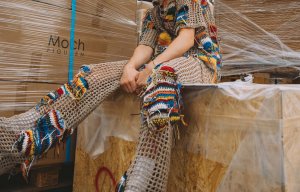
Praise for Brewed Protein at Pitti Immagine
Innovation in Textiles talks to Simardev S. Gulati, co-founder and CEO of protein fibre developer Bloom Labs.
4th September 2023
Innovation in Textiles
|
New York City
Through a combination of bio-manufacturing, advanced protein engineering and molecular biology, Bloom Labs has developed a proprietary technology capable of transforming waste into practical and versatile pellets high-performance fibres that mimic the properties of existing materials. When integrated into existing production processes, they would represent another route to eliminating the feedstock risks and ecological impact associated with oil-based raw materials.
Innovation in Textiles: Can you tell us a little about the background to the formation of Bloom Labs, who’s involved and what their backgrounds and specialisms are?
Simardev S. Gulati: Bloom Labs comprises an expert team of interdisciplinary scientists who are all leaders in their respective fields – including the inventor of plasticized protein, Walter Schmidt. Combined, we have over 100 years of science and technology expertise and the patents to prove it.
On graduating from university, I began producing clothing for major brands such as Nike, Under Armour, LuluLemon, JCPenney and others. After witnessing the harmful impact of the textile industry first hand, I have subsequently devoted my efforts to creating materials that are better for human health – and the planet.
Before working on protein fibres, I launched Dropel, a textile technology company that develops, manufactures and licenses sustainable treatments for natural fabrics. The most recent success of Dropel was in re-engineering cotton. Dropel patented and created a water and stain-proof coating technology that is certified to be free of perfluorocarbons, nanoparticles and harmful toxins. The manufacturing process for the coating adheres to the highest standards of environmental sustainability and is bluesign certified.
IIT: The Bloom Labs technology “plasticizes waste, regenerating it into uniquely practical and versatile pellets”. Can you say a little more about how this works?
SG: In theory, it is similar to recycling where you are taking something and repurposing it. In practice, we have been successfully experimenting with ways to harness the value of natural waste by-products, a protein-rich and globally abundant raw material, to create new high-performance textile and plastic materials that are scalable and commercially viable yet avoid the use of finite raw materials and their harmful extraction processes.
We are using the same processes as those used to create conventional fossil fuel-based thermoplastics, but with natural waste proteins as the raw material instead of fossil fuels. This means our technology can transform proteins into melt-spinnable fibres. We use melt-spinning machines – the same machines that polyester is produced on – which are among the most efficient production processes on earth with a throughput faster than the speed of sound at 10,000 metres per minute.
IIT: What waste feedstocks are suitable for the process?
SG: Bloom Labs sources protein waste from the textiles, materials manufacturing and food industries. Globally, there are over 15 billion pounds of protein waste produced per year, and four billion in the United States. One of the current main sources is waste feathers from bedding and pillow manufacturers.
Our technology can transform any natural found proteins into melt-spinnable fibres, designed to emulate the properties of current market-leading materials such as cotton, silk and polyester.
IIT: Are 100% polyester fibres possible from the Bloom Labs pellets?
SG: It’s important to iterate that the Bloom Labs fibre is not a polyester fibre. While the Bloom Labs fibre can emulate the properties of other fibres it is protein based.
The pellets are the same size and consistency of pellets that you would get from wool, silk, cotton, polyester in the current system, and which are fed into the same machines manufacturers currently use to produce fibres. Those fibres are then woven and spun to create textiles and apparel, there is no difference to be felt by the consumer, the fibres feel the same as ones currently being worn.
IIT: What stage are you currently at in scaling the use of Bloom Labs fibres?
SG: The Bloom Labs team is currently innovating and refining in a laboratory in New York. In 6-12 months, we will establish a pilot facility with the ability to produce 1.2 million kg a year, then move to manufacturing scale to produce 12-14 million kgs a year per facility.
Bloom labs is in conversations with several brands in the luxury and sportswear space to integrate this innovation into their supply chains.
Our mission is to make circularity an actuality. We see a future where old resource-intensive processes are replaced with cutting-edge sustainable alternatives.
Business intelligence for the fibre, textiles and apparel industries: technologies, innovations, markets, investments, trade policy, sourcing, strategy...
Find out more