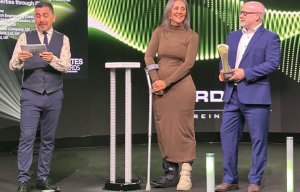
JEC recognition for Longworth’s Deecom
Longworth’s Deecom process gently removes a range of organic materials from composite fibres.
5th January 2023
Innovation in Textiles
|
Blackburn, United Kingdom
Following success in a project for recycling carbon composites with its multi-patented Deecom ‘pressolysis’ process, Blackburn, UK-based B&M Longworth is part of a new consortium which will explore the recycling of glass fibre composites.
The Emphasizing Project has received funding from Innovate UK and in addition to Longworth, will involve partners the Brunel Composites Centre (Brunel University London), EMS Chemie, Ford, Gestamp UK, Gen2Plank and TWI.
It will assess, process and analyse materials from wind turbine blades, as well as automotive and marine parts to create roadmaps for recycling. The consortium will work to demonstrate the feasibility of fabricating automotive end products from upcycled glass fibre materials, including a technical step change from established processes such as pyrolysis and solvolysis, with Deecom technology.
This pressolysis process enable the high-yield reclamation of high-quality, clean, reusable fibres that are free from residues and have a retained length and properties akin to virgin materials. The recovered, clean fibres will then be upcycled through resizing. It is hoped that through finding several use cases for the resized material, the industry will have access to a brand new, advanced material that would be on-shored and readily available at a low cost.
Glass fibre reinforced plastic (GFRP) makes up the majority of the global £54.5 billion composites market and the construction, infrastructure and transport sectors are large-scale users, accounting for 70% of the one million-plus tons of GFRP produced annually in Europe alone. In addition, the wind energy sector is expected to decommission 40,000-60,000 tons of composite wind blade material over the next two years, further adding to the amount of GFRP waste.
Intact carbon tows
The Emphasizing project builds on the success of the UK project involving B&M Longworth, the National Composites Centre and Cygnet Texkimp in demonstrating the recovery of intact tows from a carbon fibre over-wrapped pressure vessel using pressolysis.
This achievement received the Innovation in Composite Materials award at the 2022 Composite UK Industry Awards.
Cygnet Texkimp was able to reuse the tows in the manufacture of a new pressure vessel and now plans to commercialise the technology worldwide.
Using a combination of compression and decompression cycles or ‘pressure swings’, Longworth’s Deecom process gently removes a range of organic materials from composite fibres, effectively reversing the bond between fibre and matrix. The process takes place in a pressure vessel filled with superheated steam.
Depending on the polymer type, temperatures above 200°C will melt or soften the polymer and a degree of hydrolysis will occur. When at pressure, the steam will penetrate fissures in the polymer where it condenses before, upon decompression, it boils, causing an instant physical fracturing of the polymer chain and carrying away monomers and oligomers along with polymer fragments from the outer faces.
Since the process interacts with the resins rather than the fibre, it has been demonstrated to reclaim format, length and structure of post-industrial or end-of-life waste composites, whether cured or uncured. Energy use may be high due to long duration, high temperature pressure cycling, though likely to be still much lower than virgin carbon fibre manufacturing energy. The benefits of being able to recover long tows intact are significant.
Business intelligence for the fibre, textiles and apparel industries: technologies, innovations, markets, investments, trade policy, sourcing, strategy...
Find out more