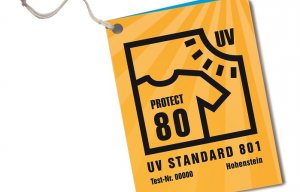
Understanding UV protective clothing
In a joint AiF research project, the Hohenstein Institute wanted to develop a more efficient finish which could be applied to lighter textiles.
20th October 2015
Innovation in Textiles
|
Boennigheim
In a joint AiF research project, the Deutsches Textilforschungszentrum Nord-West (DTNW) and the Hohenstein Institute studied new finishes for protective clothing for welders that would be repellent to splashes of molten metal.
The aim was to improve the protective effect and the wearing comfort, while retaining adequate resistance to washing in industrial textile care conditions. They investigated the effect of coatings based on inorganic-organic hybrid polymers and the use of hollow microspheres and ground carbon fibre as additives in organic coatings.
As well as improving the protective effect, the researchers have demonstrated that the newly developed finishes do not affect the wearing comfort of the fabric.
Existing protective clothing for welders normally consists of tightly woven cotton material that has a very high weight per unit area and poor breathability. The splashes of molten metal that occur during welding are normally only shortly exposed to the protective clothing. Those splashes can be at temperatures higher than 1600°C and so they damage the fibres of the clothing.
Alternative protective clothing for welders, made of high-performance fibres like meta-aramids, does offer better temperature resistance and can therefore offer a similar protective effect with less weight per unit area, but it is very expensive and therefore not widely used on the market.
The researchers' objective was to develop a finish for protective clothing for welders that would be extremely stable and resistant to thermal and oxidative influences.
The finish should also encourage the liquid metal to run off as quickly as possible before the fibres can be damaged. They wanted, therefore, to develop a more efficient finish which could be applied to lighter textiles, so that they were still comfortable to wear.
In the first stage, the DTNW researchers produced thin layers of a material with a high inorganic share and particularly good thermal resistance. They used metal oxides like silica, alumina or zirconium oxide, which have melting points higher than the temperature of molten steel. Applying these thin, thermally resistant layers did not have any relevant insulating effect, so no significant improvement in the protection for welders under DIN ISO 9150 was recorded.
To improve the protective effect, the amount of heat reaching the body has to be reduced. In the light of this, the contact time between the textile and the hot motel metal needs to be shortened. In the next stage, functional silanes and other additives were added to the base solutions, resulting in a reduction in the surface energy. This finish enabled textiles in commercial use to be put in a higher protection class.
Tests were also carried out at the Hohenstein Institute on finishes using organic polymers such as silicon and fluorocarbon in which ceramic hollow microspheres and carbon fibres were incorporated. When hollow microspheres were used, there was no improvement in the repellent effect on splashes of molten metal. However, the addition of ground carbon fibres did improve the protective effect on lightweight fabric.
The findings from the research work so far offer some promising leads for the future development of more lightweight protective clothing, Hohenstein Institute reports.
On a trial basis, the researchers have also carried out some preliminary tests involving the production of specially structured surfaces. This allowed the protection class to be improved without the use of fluorinated additives.
A follow-on project by the DTNW and the Hohenstein Institute is due to investigate this new approach, as well as the interaction of the thermally conductive coating using organic binder systems.
Business intelligence for the fibre, textiles and apparel industries: technologies, innovations, markets, investments, trade policy, sourcing, strategy...
Find out more