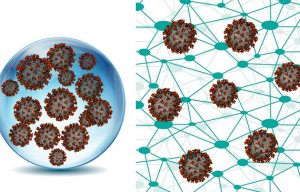
Capture Coating effectively kills Covid-19 indoors
Variant only deadly to mice was employed.
25th May 2021
Innovation in Textiles
|
California
A study carried out jointly by engineers at UC Riverside and The George Washington University – believed to be the first to employ actual coronavirus aerosols – has proved that a filter made from polymer nanofibres can capture up to 99.9% of them.
To date, all studies on mask or filter efficiency have used other materials thought to mimic the size and behaviour of coronavirus aerosols. The new study improved on this by testing an aerosolised saline solution and an aerosol that contained a coronavirus in the same family as the virus that causes Covid-19, but only infects mice.
“Previous studies have used surrogates of saline solution, polystyrene beads and bacteriophages – a group of viruses that infect bacteria,” said assistant professor Yun Shen of UC Riverside.
The study compared the effectiveness of surgical and cotton masks, a snood and electrospun nanofibre membranes at removing coronavirus aerosols to prevent airborne transmission.
The cotton mask and snood removed between 45-73% of the coronavirus aerosols and the surgical mask 98%, but the nanofibre filter was found to remove almost all of them.
Shen and George Washington University colleague Danmeng Shuai produced the nanofibre filter by an electrospinning process which created pores only a couple of micrometres in diameter on the nanofibre’s surfaces.
The group’s nanofibre technique is said to be cost effective and could be used to mass produce nanofibre filters for PPE and air filtration systems, although to date, ecisiting electrospinning techniques have proved too slow and expensive. It also provides the nanofibres with an electrostatic charge that enhances their ability to capture aerosols, and their high porosity makes it easier to breathe wearing electrospun nanofibre filters.
“Electrospinning can advance the design and fabrication of face masks and air filters,” Shen said. “Developing new masks and air filters by electrospinning is promising because of its high performance in filtration, economic feasibility, and scalability, and it can meet on-site needs of the masks and air filters.”
The team’s findings have been published in Environmental Science & Technology Letters.
Business intelligence for the fibre, textiles and apparel industries: technologies, innovations, markets, investments, trade policy, sourcing, strategy...
Find out more