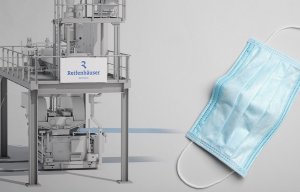
Reifenhäuser Reicofil shortens delivery for meltblown lines
Both spunbond technology and meltblown technology have been newly developed for the RF5 platform.
7th April 2017
Innovation in Textiles
|
Troisdorf
Reifenhäuser Reicofil, a leading Germany based machine supplier, has launched the new line generation RF5 for the production of spunbond, meltblown and composite nonwovens at the INDEX17 trade fair, which took place in Geneva, this week.
Both spunbond technology and meltblown technology have been newly developed for the RF5 platform and complemented by an additional technology for the first time more than 15 years of RF4. “Venturing into the market with a new technology after 15 successful years is always an exciting moment. For me personally the launch of RF5 is especially exciting because we are making a big step forward with the new performance data and the new and fascinating possibilities that arise from digitalization,” said Markus Müller, Sales Director at Reicofil.
“RF5 enables our customers to produce nonwovens on the next quality and productivity level. And the best is: even customers with existing Reicofil lines will have the possibility to benefit from some of the new advantages. We are developing amazing upgrades for RF3 and RF4 lines.”
One of the highlights of RF5 is the significant reduction of failures within the nonwoven, according to the manufacturer. When running standard raw materials, hard pieces will be reduced by up to 90% in comparison to RF4 technology. By this Reicofil says it provides a solution for one of the major issues of contamination that exists in the industry.
RF5 Technology also aims to fulfil the market demand for finer filaments: the technology is said to produce up to 20% smaller fibre diameters. Thereby titers lower than one denier are producible for the first time. Compared to the RF4s technology, the same titers can be achieved with higher outputs or finer titers are feasible with the same outputs, but can provide for better uniformity, strength and softness, the company explains.
In terms of productivity, the RF5 technology also raises the bar significantly: the output increases by up to 35 percent – to up to 270 kg/h per meter beam width for spunbond and to up to 70 kg/h per meter beam for meltblown. So, producers can run their lines at maximum speed even for higher grammages.
The meltblown technology benefits from the increased output by a much wider process window, which raises the flexibility, according to the manufacturer. Producers can decide now depending on their requirements whether to use the maximum output capacity and increase productivity by up to 35%, or to produce 20% higher meltblown quality at the present throughput levels.
When it comes to energy efficiency, Reicofil says it’s been able to reduce the specific energy consumption with every new line generation. For the production of composite nonwovens RF5 is said to save up to 15%, compared to RF4.
Business intelligence for the fibre, textiles and apparel industries: technologies, innovations, markets, investments, trade policy, sourcing, strategy...
Find out more