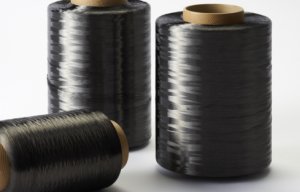
Stronger and lighter Toray carbon
The approach is based on an innovative technique for spinning polyacrylonitrile (PAN), an organic polymer resin used to make carbon fibres.
21st August 2015
Innovation in Textiles
|
Atlanta, GA
The work is part of a four-year, US 9.8 million project, sponsored by the Defense Advanced Research Projects Agency (DARPA), to improve the strength of carbon-fibre materials.
“By using a gel-spinning technique to process polyacrylonitrile copolymer into carbon fibres, we have developed next-generation carbon fibres that exhibit a combination of strength and modulus not seen previously with the conventional solution-spun method,” explained Satish Kumar, a professor in the Georgia Tech School of Materials Science and Engineering who leads the project. “In addition, our work shows that the gel-spinning approach provides a pathway for even greater improvements.”
In gel spinning, the solution is first converted to a gel; this technique binds polymer chains together and produces robust inter-chain forces that increase tensile strength. Gel spinning also increases directional orientation of fibres, which also augments strength.
By contrast, in conventional solution spinning, a process developed more than 60 years ago, PAN co-polymer solution is directly converted to a solid fibre without the intermediate gel state and produces less-robust material.
The gel-spun carbon fibre produced by Kumar’s team was tested at 5.5 to 5.8 gigapascals (GPa) – a measure of ultimate tensile strength – and had a tensile modulus (a measure of stiffness) in the 354-375 GPa range. The material was produced on a continuous carbonization line at Georgia Tech that was constructed for this DARPA project.
“This is the highest combination of strength and modulus for any continuous fibre reported to-date,” said Satish Kumar. “And at short gauge length, fibre tensile strength was measured as high as 12.1 GPa, which is the highest tensile-strength value ever reported for a PAN-based carbon fibre.”
Moreover, Kumar noted, the internal structure of these gel-spun carbon fibres measured at the nanoscale showed fewer imperfections than state-of-the-art commercial carbon fibres, such as IM7.
Specifically, the gel-spun fibres display a lower degree of polymer-chain entanglements than those produced by solution spinning. This smaller number of entanglements results from the fact that gel spinning uses lower concentrations of polymer than solution-spinning methods.
Kumar and his team convert the gel-spun polymer mix into carbon fibres via a selective treatment process called pyrolysis, in which the spun polymer is gradually subjected to both heat and stretching. This technique is said to eliminate large quantities of hydrogen, oxygen, and nitrogen from the polymer, leaving mostly strength-increasing carbon.
“It’s important to remember that the current performance of solution-spun PAN-based carbon fibres has been achieved after many years of material and process optimization – yet very limited material and process optimization studies have been carried out to date on the gel-spun PAN fibre,” Kumar said.
“In the future, we believe that materials and process optimization, enhanced fibre circularity, and increased solution homogeneity will further increase the strength and modulus of the gel-spinning method.”
Business intelligence for the fibre, textiles and apparel industries: technologies, innovations, markets, investments, trade policy, sourcing, strategy...
Find out more