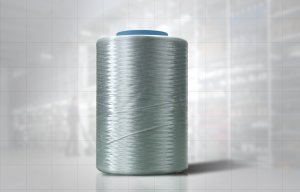
Dyneema from circular ethylene
Innovation in Textiles talks to Edwin Keh, CEO of the Hong Kong Research Institute for Textile and Apparel (HKRITA).
28th January 2019
Innovation in Textiles
|
Hong Kong
Edwin Keh, CEO of the Hong Kong Research Institute for Textile and Apparel. © HKRITA
Innovation in Textiles talks to Edwin Keh, CEO of the Hong Kong Research Institute for Textile and Apparel (HKRITA) about the latest ambitious recycling systems it is developing.
Please could you outline the key activities of the HKRITA for our readers?
Edwin Keh: HKRITA is an applied research centre for textiles, apparel and the fashion industry in Hong Kong. Our work is to foster technology breakthroughs in order to create new value for our industry and a positive contribution to society.
Over the past few years, we have made several significant breakthroughs in the development of practical recycling technologies through our research and development efforts.
We worked with Novetex Textiles to set up a system for upcycling post-consumer blended garments. The goal was to set up a mill to recycle blended textiles into new fibres and yarns which we have now done with the opening of a factory in Tai Po – Hong Kong’s first-ever textile recycling mill and the first local spinning mill to open in in half a century.
The factory also houses a large scale research project to recycle post-consumer material using our new hydrothermal system to separate cotton polyester blends. This pre-industrial system is evaluating the parameters for scaling up the treatment conditions to industrial scale. We are looking at energy consumption and the optimisation of the operation to facilitate its commercialisation process. This project is collaboration between HKRITA and the H&M Foundation.
Another recycling system is a “garment to garment” direct to consumer project (the G2G recycled system) set up at The Mills – a revitalization project for a cluster of disused cotton mills in Tsuen Wan, Hong Kong. The G2G recycled system is a mini-scale production line that recycles post-consumer garments into clean and wearable clothes again. Consumers are able to see in real time how their old clothes can be turned into new ones. You can see some information about this here.
HKRITA is an applied research centre for textiles, apparel and the fashion industry in Hong Kong. © HKRITA
At HKRITA we want to drive innovation and facilitate collaboration. We have been organising our flagship Innovation and Technology Symposiums for the industry since 2007. The latest edition took place on September 7th 2018. With the theme The Re-imagination of Our Industry – Building on Our Heritage for Tomorrow’s Breakthroughs, the event attracted more than 600 participantsincludingpublic officials, industry leaders, entrepreneurs, startups and members of the sustainable community. Industry and research leaders such as Karl-Johan Persson, CEO of H & M Hennes&Mauritz, Dr Carlo Imò, president of Kering Asia Pacific and Professor David Bell, former chaired professor of marketing at the Wharton School of the University of Pennsylvania spoke. (For the 2018 symposium archive, click here)
We have kept close contact with different stakeholders along the innovation chain. Recently, HKRITA arranged technology demonstrations and site visits for principal officials of the Hong Kong Special Administrative Region, as well as R&D and industry counterparts such as the Hong Kong University of Science and Technology, the Royal Swedish Academy of Engineering Sciences, and Federation of Hong Kong Industries among others.
Since our inception in 2006, we have received 58 international and local awards. In 2018 alone, we won 14 awards. These include five gold medals, one silver medal in the 2018 International Exhibition of Inventions of Geneva and special prize from The National Research Council of Thailand.
How did the project for the development of the Novetex Upcycling Mill for the H&M Foundation and Novetex come about?
EK: As a leading yarn spinner, Novetex Textiles is committed to sharing the responsibility of environmental protection and to supporting Hong Kong’s innovative technologies. HKRITA has been working with Novetex to develop the production-level textile upcycling system since 2017. The mechanical recycling system provides a safe and dry process to upcycle textile wastes into quality textile fibre which can then be used in the production of yarn, fabric and garments.
The goal of HKRITA to drive innovation and facilitate collaboration. © HKRITA
The factory also provides a test bed for the pre-industrial scale hydrothermal system, a collaboration between HKRITA and the H&M Foundation who kicked off a four-year partnership in September 2016 to develop recycling and circular technologies. A series of projects, with the aim of closing the loop for the textile, apparel and fashion industries have been ongoing ever since. The hydrothermal system is one of them. When completed, this technology will be made available for all users.
When did the project start and where are you with it now?
EK: Production-level textile upcycling system started in 2017. Currently one production line is installed in the factory which can produce one ton of fibre a day. Two more one-ton production lines will be installed and become operational in the next few months.
The hydrothermal system developed from lab-scale to pre-industrial scale in 2016. The pre-industrial system is being used to evaluate the parameters for scale-up, such as the treatment conditions in a scale of 500L, energy consumption, and optimization of operation. This will see the system’s industrialisation in the future.
Was its location in Hong Kong chosen simply because that’s where you’re located?
EK: Circularity and post-consumer recycling of apparel is a challenge for most developed cities in the world like Hong Kong. According to most authoritative sources, Hong Kong produces about 250 tons of garment waste every day. Many big cities like Hong Kong no longer have a manufacturing base. There are logistic inefficiencies to moving post-consumer mixed material apparel across vast distances.
Over the past few years, HKRITA made several significant breakthroughs in the development of practical recycling technologies. © HKRITA
There are also legal barriers to crossing national borders. Our hydrothermal system is designed to solve these problems by using a small highly efficient system that can separate mixed yarn fabrics and get treated materials back to staple and yarn. In this form, these now useful materials can be efficiently transported for processing. So Hong Kong is the perfect test bed for this recycling technology.
Could you say a little more about this hydrothermal system?
EK: Cotton and polyester blended-fibre fabrics are today the most used materials for apparel. These materials are great to enhance fit, style and comfort and they are also the most commonly disposed of in apparel.
The hydrothermal system can efficiently separate blended materials, to make “closed-loop recycling” possible. Cotton and polyester blends – fibres with different properties – can be efficiently separated and recovered for re-use. The whole process uses only heat, water and less than 5% of a biodegradable green chemical to achieve a recovery rate of over 98% for polyester fibres in 0.5-2 hours. The separated polyester material is recovered in fibre form, ready for spinning and manufacturing into new fabric. So there is now no need for additional complex treatments like polymerisation and melt spinning. Cellulose is separated and recovered in powder form. This material is decomposed from cotton and can be applied to functional products that require super-absorbency materials or can be regenerated into cellulose fibres.
The Upcycling Mill is also carrying out mechanical recycling. What new developments have you introduced to what is basically a traditional and long-established process?
EK: Mechanical recycling is the most mature textile recycling method. However, it causes deterioration of the recycled fibres, so processed materials end up in low value applications such as rags, insulation, floor covering, or fill material. Mechanical recycling methods also do not guarantee the hygiene of the reproduced fibre.
Our upcycling system recycles old clothes into quality textile fibers in a dry and closed condition in which the textile fibers are hygienic, to be used for the re-production of various yarn, fabric, and garments. The used garments are cleaned at the beginning and towards the end of the process with ozone and ultra-violet (UV) sanitization systems to ACHIEVE a minimum of +90% reduction of microorganism concentration on the material.
HKRITA works to foster technology breakthroughs in order to create new value for the industry. © HKRITA
In addition, during the downstream process, fibre quality and properties are maintained through a series of special mechanical processes.
At last year’s Dornbirn-GFC in Austria, you spoke of the key challenges associated with post-consumer textile recycling in the areas of science, engineering, logistics and establishing a strong enough business case. Can we start with the science? What’s really needed here to move things forward?
EK: Applied challenges require applied solutions. These are usually cross disciplined in nature. All known recycling methods – mechanical, chemical and biological – have their drawbacks. In the challenge of the recycling of textiles, we first have to develop methods to treat materials in a benign, safe, efficient and cost effective manner. Blended materials have to be separated, mechanical strength needs to be preserved, and hand feel and performance properties have to be enhanced. The challenge is to find the treatment processes that can accomplish these goals, and scale this to a level that is useful to industry. So we work with material scientists to understand the properties of the materials we want to treat, separate, and recover. We also need to discover solutions that are broad enough to work on a wide range of material weights and compositions.
As far as engineering is concerned, I believe you had to recruit from Japan. Is this just a problem in Hong Kong?
EK: Recycling and circularity are significant and pressing challenges for our industry and our world. We wanted to get to scalable solutions as quickly as possible. To this end we wanted to work with the best and most experienced engineers we can find. This is why our Hong Kong engineering team went to Japan. HKRITA has been working in Japan on various projects for over seven years. We have a good working relationship with several Japanese universities.
Is the sheer complexity of international textile and apparel chains the main logistical challenge?
EK: Our industry’s current global manufacturing supply chain is optimized to making products in the less developed economies for consumption in the developed economies. So a big barrier to the reuse of apparel is that the materials for recycling are in the wrong place. As a consequence, there is a logistic challenge to transport things to the right processing location in a cost effective manner. Pre-consumer we have multiple challenges to ensure we design with circularity as our intention, process materials in a transparent and responsible manner, and manufacture in ways to support deconstruction and repurposing.
And what about the business case?
EK: While consumers desire to support sustainability, they also want great value, convenience, the right trends and comfortable products. Our challenge is to deliver all of these using recycled and repurposed materials with no additional cost and no sacrifice in performance. Until costing is done differently, our goal is to deliver comparable to new material quality at below new material prices. By developing the hydrothermal system, we are getting closer to delivering on this.
Finally, at Dornbirn you also expressed the view that the targets for recycling initiatives are set too far into the future. Can you expand on this?
EK: Circularity and recycling in the textile, apparel and fashion industry is difficult and complex. Many companies in our industry have an ambition to become more sustainable. Yet this is so difficult within their current business model that they can’t deliver or deliver quickly. As result many announce aspirational goals set in the far distant future. We hear often goals set five, ten, or twenty years in the future. The fear is that this type of goal setting may also be a way to defer the problem for now. The danger is that it also becomes a reason to do nothing. Today’s long term goal may then become the next person’s problem.
Business intelligence for the fibre, textiles and apparel industries: technologies, innovations, markets, investments, trade policy, sourcing, strategy...
Find out more