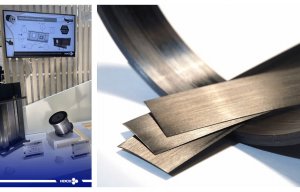
Thermoplastic success for aerospace
The global potential for components produced with the freespace composite manufacturing system is estimated with approximately USD 2-3bn in 2016.
20th November 2014
Innovation in Textiles
|
Singapore
Composite Cluster Singapore (CCS) has developed a concept that aims to manufacture high-performance composite structures in shorter time and with significantly reduced cost.
The groundbreaking concept builds on market proven thermoplastic tape placement technology and integrates it with advanced robotics and laser technologies to overcome limitations of current solutions.
CCS will continue the development in a project, jointly with its partners HOPE Technik, KUKA Robot Automation (M), SGL Group and TRUMPF.
“Identifying and supporting innovative, high-growth start-ups is at the heart of our efforts. The success of the project will push the boundaries in materials engineering in Singapore and have disruptive implications in the high-technology based manufacturing for the aerospace, aviation and motoring industries,” explained Edwin Chow, Executive Director for the Innovation and Start-ups Group, Standards, Productivity and Innovation Board (SPRING) Singapore.
“Partnering with local and international industrial leaders, CCS has assembled a capable team to ensure the project’s quality and eventually bring this groundbreaking solution to the market.”
“The idea of freespace composite manufacturing – that we are developing further in this project – is certainly pushing the boundaries of what is possible with today’s technology,” said Dr Florian Doetzer, MD, CCS.
“It is the joint competence of world class project partners that will allow us to achieve something that has never been done before. As bold as the idea is, this is the team to do it. And it will be done in Singapore.”
“We leverage on our extensive background in composites manufacturing and mixed it with the robotics capability we have to work towards this truly game-changing manufacturing process,” commented Peter Ho, CEO, HOPE Technik.
Parts and components made from high-performance carbon fibre reinforced polymers (CFRP) generally have superior stiffness and strength per weight when compared to metal components.
In addition, they also present opportunities in design and shapes, because they are per definition an additive manufacturing method. CCS and its partners are building on the recent advancements in materials, as well as automation to establish a process and machine concept to manufacture CFRP components without expensive moulds and tooling.
The CCS project team will be lead by Dr Florian Doetzer, Managing Director of Composite Cluster Singapore (CCS), an experienced technology manager with previous positions in automotive and aerospace industries. He and his team will be supported by each partners’ specialist engineers in their respective field of expertise: integration and prototyping (HOPE), robotics (KUKA), thermoplastic composite material (SGL) and industrial laser technology (TRUMPF).
This will target a global market of high-performance composites that Freedonia Group estimates with USD 10.2bn in 2016, while Visiongain estimates the global market for aerospace components with USD 10.3bn in 2012.
The global potential for components produced with the freespace composite manufacturing system is estimated with approximately USD 2-3bn in 2016 spanning multiple industries, such as aviation, space, marine, racing and sports.
Business intelligence for the fibre, textiles and apparel industries: technologies, innovations, markets, investments, trade policy, sourcing, strategy...
Find out more