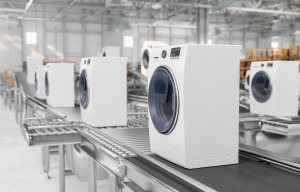
Eliminating microplastics in household washing
A collection system similar to deposit returns for drink containers could be developed for the household waste.
24th June 2021
Innovation in Textiles
|
Kaunas, Lithuania
A team of scientists from Kaunas University of Technology (KTU) and the Lithuanian Energy Institute are proposing a method of converting the lint microfibres found in clothes dryers into energy.
The team has not only constructed a pilot pyrolysis plant but also developed a mathematical model to calculate the possible economic and environmental outcomes.
It is estimated that by converting lint microfibres produced by a million people, almost 14 tons of oil, 21.5 tons of gas and nearly 10 tons of char could be produced. These would be worth around €100,000 on the open market and their recycling would achieve a carbon footprint reduction of 42,039,000kg CO2-eq/t.
Large quantities of microplastic are being washed down our drains and enter our seas threatening the environment
Each year, the global population consumes approximately 80 billion pieces of clothing and approximately €140 million worth of it goes into landfill. This is accompanied by large amounts of emissions, causing serious environmental and health problems. One of the ways to lessen the footprint of consuming clothes is to reduce the impact of laundry. During the machine-washing of a garment, around 300mg of microfibres are generated from 1kg of textile.
“Lint microfibres are classified as microplastics and whereas large plastic items can be sorted out and recycled relatively easily, this is not the case with microplastic – tiny plastic pieces, less than 5mm in diameter,” says Dr Samy Yousef, a researcher at KTU’s Faculty of Mechanical Engineering and Design. “Large quantities of microplastic are being washed down our drains and enter our seas threatening the environment.”
Pyrolysis
Lint microfibres from the filters of the drying machines in the dormitories of KTU were collected for the research..
Using a pilot pyrolysis plant, built at the laboratories of Lithuanian Energy Institute, the scientists were the able to extract three energy products – oil, gas and char – from the collected lint microfibre batches. When treated thermally, the lint microfibres decompose into energy products with around a 70% cent conversion rate.
“When we think about textile waste, we usually imagine garments which are contaminated with dye and dirt,” Yousef says. “Much energy is needed to turn them from solid waste into liquid. However, lint microfibre is broken-down fibre textile waste – it has a uniform size and shape, contains a lot of flammable compounds in the cotton and polyester elements and its transformation is easier.”
The KTU study shows that if applied on an industrial scale, the strategy is profitable and eco-friendly.
“I believe that the collection system – similar to deposit returns for drink containers – could be developed based on our research,” Yousef says. “A household would bring the lint microfibre from the drying machine filters to a collection point and receive some kind of compensation for it. We have proposed the technology and made calculations, which may be developed further.”
Yousef and his research group have developed other green/eco-friendly technologies to extract cotton, glucose and energy products from textile waste and end-of-life euro banknotes using mechanical, thermal, chemical and biological treatments.
Business intelligence for the fibre, textiles and apparel industries: technologies, innovations, markets, investments, trade policy, sourcing, strategy...
Find out more