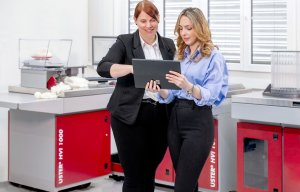
Uster focus on quality at ITM 2024
Subscription service combines end-to-end yarn quality software along with expert ongoing assistance.
27th January 2025
Innovation in Textiles
|
Uster, Switzerland
Uster’s FiberQ automated raw material management system has enabled leading Indian yarn spinner Sagar Manufacturers to achieve 2,000 consistent fibre laydowns in a single year.
In each laydown, between 70-100 fibre bales are mixed to be fed into the the bale openers and FibreQ supports their correct selection to ensure consistent yarn quality and optimised process efficiency over a set period of time, as well as day-to-day consistency in all operations and the automation of many tasks previously done manually.
Sagar’s plant in Tamot, Madhya Pradesh, comprises six spinning units with an installed capacity of 23,0784 for annual production of around 52,780 tons of yarn, in addition to a knitting unit.
The company has been one of the first adopters of FiberQ, which is provided as an annual subscription combining the software and advisory services from expert Uster technologists.
Sagar’s figures show that using this system, yarn realisation has increased by between 0.3-0.5% on average and it has also eliminated the need for cutting and creeling – a big advantage in terms of efficiency and fewer changes in production. This equates to a payback period of just three months.
“Uster FiberQ is a game-changer in terms of high-quality consistency with minimal production cost,” says A.K. Saini, Sagar’s chief general manager of operations. “We have seen better fibre utilisation, significantly improved yarn quality consistency and the elimination of faults such as white specks and barré. At the same time, we have achieved zero quality complaints from our customers. These outstanding results have convinced our management about the value of FiberQ and we have now confirmed the renewal of the subscription.
“Uster’s end-to-end solution also offers access to continuous improvements such as supplier statistics and fibre-to-yarn correlation, which will add even more value in future. Another plus is the easily accessible laydown history and the visibility of the impact of the different cotton lots in use.”
For the textile industry, the idea of subscribing to a software service for raw material management is quite new, although it has been established for many years in other sectors.
The FiberQ advisory service ensures there is always a textile engineer with mill experience and deep knowledge available to support the spinners. As well as taking care of all aspects of installation, there are periodic assessments to track quality status from fibre to yarn, which is a highly appreciated element of the service.
“The advisory services have been extremely beneficial and we have gained insights from best practices, proven in mills worldwide, for greater optimisation opportunities,” says Saini. “At Sagar, we are convinced that the value we get from this solution completely justifies the recurring investment.”
Sagar is now providing customers with bigger yarn lot sizes with the same quality and colour properties, enabling its customers to produce larger, uniform batches of knitted and dyed fabrics and save manufacturing costs.
Business intelligence for the fibre, textiles and apparel industries: technologies, innovations, markets, investments, trade policy, sourcing, strategy...
Find out more