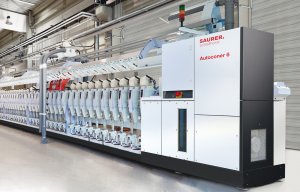
Rieter acquires Schlafhorst
Schlafhorst will present its Autocoro 9 rotor spinning machine, with intelligent individual spinning position technology.
6th May 2016
Innovation in Textiles
|
Übach-Palenberg
German textile machinery manufacturers, Saurer Schlafhorst and Saurer Zinser, will offer their spinning and winding machines of the market and textile technology leaders at the ITM16 international trade fair for textile machinery that takes place in Istanbul next month.
Schlafhorst will present its Autocoro 9 rotor spinning machine, with intelligent individual spinning position technology, which is said to contribute towards managing energy consumption, productivity, efficiency, ease of operation and quality. The machine outperforms its predecessor with 25 % lower energy consumption, 19 % reduction in spinning costs, proven rotor speeds of 180,000 rpm, take-up speeds of 300 m/min and a 60 % lower servicing outlay, the company reports.
The semi-automatic BD 6 machine is also in a league of its own, producing packages in Autocoro quality across the entire range of yarn counts and with package sizes of up to 320 mm in diameter. Its low energy consumption, rapid take-up speeds of 230 m/min and high piecing reliability are said to cut spinning costs and increase the profitability of spinning mills, according to the manufacturer.
At a length of 2016 spindles, the new Zinser 72 ring spinning machine breaks the 2000-barrier. The machine is super-long, super-economical and extremely user-friendly, the company reports. It is designed to lower production costs by up to 11% and has a footprint that is up to 21% smaller, compared with shorter rival machines, according to the company. The new two-end TwinSuction system helps save up to two-thirds of the energy consumption in combination with the sensor-controlled OptiSuction yarn break suction system.
The ZinserImpact 72 compact spinning machine is equipped with the self-cleaning Impact FX unit and aims to guarantee top productivity and optimal raw material utilisation.
The new ZinserSpeed 5A speed frame boasts an energy-saving mode for suction and flyer table blowing that shaves 20% off the total energy consumed. In 220 gauge the speed frame is also up to 17% shorter than its predecessor. With a doffing time of less than two minutes, the ZinserSpeed 5A is said to ensure maximum production efficiency.
“Intelligent sensor technology, smart process control, auto-calibration and functionally optimised processes turn the new Autoconer 6 into an automatic package winder that pushes the textile-technological limits, winding at the most productive settings virtually without the need for operators,” says the company.
Innovations, such as LaunchControl, SmartCycle, SmartJet and Speedster FX are said to boost productivity by up to 12%, compared with the previous model. The new Eco-Drum-Drive system, SmartCycle and the intelligent vacuum control system Power on demand are designed to reduce the energy consumption on the Autoconer 6 by up to 20%.
Spinning mills with POC, the Schlafhorst and Zinser Plant Control System, can use their production and quality data to improve efficiency. Service intervals can be optimised and production downtimes and quality problems avoided by prompt intervention when using the new Off-Standard analysis.
With the innovative SUN - SERVICE UNLIMITED service concept, Schlafhorst and Zinser also offer their customers support in their day-to-day operations that is unmatched by any other manufacturer. Over 500 service staff in 20 service stations and 3 technology centres advise customers with regard to productivity and quality increases, as well as energy conservation.
Business intelligence for the fibre, textiles and apparel industries: technologies, innovations, markets, investments, trade policy, sourcing, strategy...
Find out more