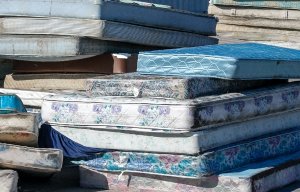
Mattress recycling scheme in Germany
Polypropylene-based materials offer superior bond strength and thermal stability without the need for additional additives.
2nd December 2024
Innovation in Textiles
|
Muttenz, Switzerland
A critical element behind the durability, comfort and sustainability of mattresses is their fabric reinforcement and lamination using high-performance polymers.
These advanced materials ensure longevity and efficiency, offering unmatched bonding capabilities, especially in fabric applications, along with significant sustainability benefits.
Muttenz, Switzerland-headquartered Clariant’s Licocene PP 1602, 2402, 2502 2602 and 3602 polymers have redefined the standards in hot melt polymers used in mattress production. Unlike traditional EVA-based adhesives, these polypropylene-based materials offer superior bond strength and thermal stability without the need for additional additives such as tackifiers or plasticizers. This leads to a reduction in VOC emissions and negligible odour, both during manufacturing and in the final product, ensuring a healthier and more comfortable sleeping environment for consumers.
One of the standout features of Licocene polymers is their ability to reduce material and energy consumption during the application process. They allow for more precise placement, meaning manufacturers can use less adhesive while maintaining strong bonds, leading to significant cost savings. Additionally, their low viscosity enables the use of smaller nozzles, which further enhances productivity by reducing downtime for maintenance and allowing for faster line speeds.
Layers
Clariant’s Licocene polymers offer a comprehensive solution for manufacturers throughout the entire mattress production process – from the initial product development phase to the final assembly,
The mattress ticking is the first line of defence against wear and tear and Licocene PP 2602 or PP 3602 are used to coat and laminate the woven ticking fabrics, locking the fibres in place to prevent seam slippage and fraying over time. This layer also allows for custom enhancements like water resistance and antimicrobial properties.
Premium innerspring mattresses also rely on pocket coils for customised support. Licocene PP 2402 and PP 2502 hot melt polymers are exceptional at fusing the fabric pockets to create the pocket spring structure. These polymers offer excellent cohesive strength while maintaining low viscosity, allowing them to thoroughly permeate all nonwoven layers. The result is a durable, consistent bond that enhances the overall quality of the mattress. This bonding solution ensures that the pocket coil system maintains its integrity, contributing to the mattress’s long-term performance and comfort.
For mattresses featuring foam comfort layers or cores, Clariant’s Licocene polymers demonstrate superior adhesion for bonding different foam components together. This ensures the mattress maintains its structural integrity over years of use. Additionally, they contribute to reduced noise levels in the finished mattress.
To prevent a mattress sliding around, Licocene PP 1602 provides excellent anti-slip properties without leaving any sticky residue, keeping a mattress securely in place on smooth surfaces.
The Licocene Terra range is meanwhile made from renewable raw materials via biomass balance certification. Some Licocene solutions also enable mono-material construction for easier recycling at end of life.
Business intelligence for the fibre, textiles and apparel industries: technologies, innovations, markets, investments, trade policy, sourcing, strategy...
Find out more