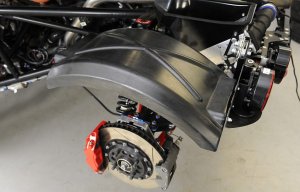
TFP extends use of carbon composites in RP1 sports car
Opinion
Liquid crystal elastomer the key to controlled heating.
30th October 2023
Adrian Wilson
|
Cambridge, MA, USA
Fibreobo is a new fibre developed at MIT that contracts in response to an increase in temperature and self-reverses once the temperature decreases, without any embedded sensors or other hard components.
The low-cost fibre is fully compatible with textile manufacturing techniques, including weaving, knitting and embroidery and can be produced continuously.
As such it could enable designers to easily incorporate actuation and sensing capabilities into a wide range of fabrics for numerous applications.
These fibres could also be combined with conductive threads, acting as a heating element, providing the user with digital control over a textile’s form. A fabric could change shape based on any piece of digital information, such as readings from a heart rate sensor.
“So much of our environment is adaptive and responsive, but textiles are completely inert,” says Jack Forman, a graduate student in the Tangible Media Group of the MIT Media Lab.
He was joined in the development by 11 other researchers at MIT and Northeastern University, including his advisors, Professor Neil Gershenfeld, who leads the Center for Bits and Atoms, and Hiroshi Ishii, Professor of Media Arts and Sciences and director of the Tangible Media Group.
Morphing materials
The MIT researchers wanted a fibre that could actuate silently and change its shape dramatically, while being compatible with common textile manufacturing procedures. To achieve this, they used a liquid crystal elastomer (LCE).
A liquid crystal is a series of molecules that can flow like liquid, but when they’re allowed to settle, stack into a periodic crystal arrangement. The crystal structures are incorporated into an elastomer network.
As the LCE material heats up, the crystal molecules fall out of alignment and pull the elastomer network together, causing the fibre to contract. When the heat is removed, the molecules return to their original alignment, and the material to its original length.
By carefully mixing chemicals to synthesize the LCE, the researchers can control the final properties of the fibre, such as its thickness or the temperature at which it actuates.
The researchers discovered, however, that making fibre from LCE resin is tricky, and existing techniques often result in a fused mass that is impossible to unspool.
Fibre fabrication
Forman built a machine using 3D-printed and laser-cut parts and basic electronics to overcome the fabrication challenges.
With this, the thick and viscous LCE resin is heated and then slowly squeezed through a nozzle. As the resin comes out, it is cured carefully using UV lights that shine on both sides of the fibre as it’s extruding.
If the light is too dim, the material will separate and drip out of the machine, but if it is too bright, clumps can form, which yields bumpy fibres.
The fibre is then coated and cured again, this time with UV lights turned up to full blast, creating a strong and smooth fibre. Finally, it is collected into a top spool and dipped in powder so it will slide easily into machines for textile manufacturing.
Ready to use
From chemical synthesis to finished spool, the process takes about a day to produce approximately a kilometre of ready-to-use fibre.
Fibreobo can contract up to 40% without bending, actuate at skin-safe temperatures and be produced with a low-cost setup for 20 cents per metre, which is about 60 times cheaper than commercially available shape-changing fibres.
The MIT researchers have used Fibreobo to demonstrate several products, including an adaptive sports bra made by embroidery that tightens when the user begins exercising.
They also used an industrial knitting machine to create a compression jacket for a dog. The jacket can actuate and “hug” the dog based on a Bluetooth signal from Forman’s smartphone.
The researchers now want to adjust the fibre’s chemical components so it can be recyclable or biodegradable and to streamline the polymer synthesis process for users without wet lab expertise.
They are also exploring other ways to make functional fibres, such as by incorporating hundreds of microscale digital chips into a polymer, utilising an activated fluidic system, or including piezoelectric material that can convert sound vibrations into electrical signals.
Business intelligence for the fibre, textiles and apparel industries: technologies, innovations, markets, investments, trade policy, sourcing, strategy...
Find out more