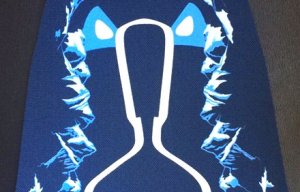
TCL 2017: Kinder chemistries and agile approaches
Opinion
New technique is based on a foamed ink formulation.
22nd March 2021
Adrian Wilson
|
Putian, China
Over 300 million pairs of sports shoes have now been produced by the major brands such as adidas, Columbia, New Balance and Nike, exploiting the surface looks provided by the standard haptic coating technology developed by Huafeng, headquartered in Putian, China.
At the recent online World Congress on Textile Coating (WCTC), Huafeng’s director of innovation and creation Thomas Schmidt introduced a number of new innovations the company is currently developing, including haptic cushion coating.
The standard haptic coating technology is a method of adding a huge range of surface designs to textile surfaces for both footwear and apparel. They are in thicknesses of between 0.2-1.2mm and can be in any colour combination.
Additive process
Huafeng’s coating process involves an additive, layer-by-layer approach based on a modified screen printing process and work is currently underway to fully digitise it. At present, however, the step-by-step process still ensures zero cutting waste.
Haptic coating technology has been highly successful due to its unlimited design options, high material efficiency, no cutting waste and fully water-based chemistry
The coatings are based on polyurethane chemistry exploiting a crosslinked polymer to provide strong bonding, durability, abrasion resistance and other beneficial properties. The chemistry is completely water based with high solids content for maximum effectiveness.
“We are formulating and manufacturing our own inks to be fully in control and ensure our coatings are fully water based and safe,” Schmidt said. “Elaborate 3D patterns are created with not only any colour combination, but graded thicknesses and modified surfaces, since we are all about touch.”
Foamed ink
The new haptic cushion coating technique is based on a new foamed ink formulation, which combined with the company’s in-house one-shot printing technique now allows for the creation of surface designs that can be up to 5mm in thickness with a very smooth round appearance and can achieve up to 40% weight savings due to their foamed production.
Glow in the dark effects have also been produced with the incorporation of fluorescent pigments.
With its Haptic Cushion Reborn concept, Huafeng has also developed two approaches to recycling garments into either coarse or fine particles to be used in the coatings.
The company has accelerated its globalisation efforts during the Covid-19 pandemic, adding new offices to its network, and is also planning to open its first manufacturing plant outside its Chinese HQ in Vietnam.
“Our haptic coating technology has been highly successful due to its unlimited design options, high material efficiency, no cutting waste and fully water-based chemistry,” Schmidt concluded. “With haptic cushion technology we are further expanding the potential for many successful and sustainable new designs.”
Business intelligence for the fibre, textiles and apparel industries: technologies, innovations, markets, investments, trade policy, sourcing, strategy...
Find out more