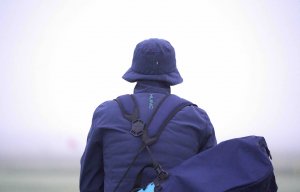
HLINC opts for eVent BIO
Scientists from RMIT University have developed a scaleable method for rapidly fabricating textiles that are embedded with energy storage devices.
27th August 2019
Innovation in Textiles
|
Melbourne
The new technology can produce a 10x10cm smart textile patch in just three minutes. © RMIT University
The next generation of waterproof smart fabrics can be laser printed and made in minutes. Scientists from RMIT University have developed a cost-efficient and scaleable method for rapidly fabricating textiles that are embedded with energy storage devices. In just three minutes, the method can produce a 10x10cm smart textile patch that’s waterproof, stretchable and readily integrated with energy harvesting technologies.
The technology enables graphene supercapacitors – powerful and long-lasting energy storage devices that are easily combined with solar or other sources of power – to be laser printed directly onto textiles, the scientists explain.
In a proof-of-concept, the researchers connected the supercapacitor with a solar cell, delivering an efficient, washable and self-powering smart fabric that overcomes the key drawbacks of existing e-textile energy storage technologies.
The growing smart fabrics industry has diverse applications in wearable devices for the consumer, health care and defence sectors - from monitoring vital signs of patients, to tracking the location and health status of soldiers in the field, and monitoring pilots or drivers for fatigue.
Dr Litty Thekkakara, a researcher in RMIT’s School of Science, said smart textiles with built-in sensing, wireless communication or health monitoring technology called for robust and reliable energy solutions.
Dr Litty Thekkakara, RMIT researcher and co-developer of new technology for rapidly fabricating textiles embedded with energy storage devices. © RMIT University
“Current approaches to smart textile energy storage, like stitching batteries into garments or using e-fibres, can be cumbersome and heavy, and can also have capacity issues,” Dr Thekkakara said. “These electronic components can also suffer short-circuits and mechanical failure when they come into contact with sweat or with moisture from the environment. Our graphene-based supercapacitor is not only fully washable, it can store the energy needed to power an intelligent garment – and it can be made in minutes at large scale.”
“By solving the energy storage-related challenges of e-textiles, we hope to power the next generation of wearable technology and intelligent clothing.”
The research analysed the performance of the proof-of-concept smart textile across a range of mechanical, temperature and washability tests and found it remained stable and efficient.
RMIT Honorary Professor and Distinguished Professor at the University of Shanghai for Science and Technology, Min Gu, said the technology could enable real-time storage of renewable energies for e-textiles: “It also opens the possibility for faster roll-to-roll fabrication, with the use of advanced laser printing based on multifocal fabrication and machine learning techniques.”
Business intelligence for the fibre, textiles and apparel industries: technologies, innovations, markets, investments, trade policy, sourcing, strategy...
Find out more