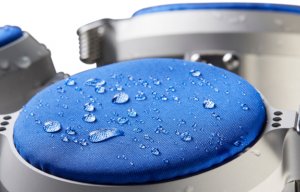
A sustainable solution for water repellency testing
In a sequence of 150 tests, consumption is reduced from from 2,100 litres to just 23 litres.
2nd May 2023
Innovation in Textiles
|
Halifax, United Kingdom
UK-based textile testing solutions provider James Heal has reduced the volume of waste water and energy consumed by its TruRain water repellency textile tester to a fraction of that of competing products.
Water repellency is an important function of technical fabrics from a safety and comfort perspective, in garments intended to protect the wearer in wet conditions. The Bundesmann test is the established industry-wide method of providing artificial rainfall, simulating the natural outdoor environment to determine the water repellency of different fabrics and garments.
Around for many years, Bundesmann testing instruments have a high environmental impact through heavy water usage and energy consumption, which adds up to high running costs, and they also have a reputation for being difficult and messy to use.
James Heal saw an opportunity to make improvements through better technology and design, by focusing on the day-to-day challenges of the user.
The result is TruRain, the next generation Bundesmann tester with a water recirculation unit. In comparison to the traditional options on the market, the system uses 99% less water during testing based on a weekly programme of conducting 150 tests, reducing consumption from 2,100 litres to just 23 litres.
In addition, TruRain makes significant energy cost savings over a typical eight-hour shift which sees an 83% total cost reduction. Productivity is also increased through greater ease of use than a traditional Bundesmann, since tests can be run continuously for a week without the need to change the water. An automated shower guard that protects the operator from getting wet during testing is also being welcomed by lab technicians using the instrument.
“TruRain is a game-changer for sustainably-conscious brands and manufacturers who are looking to improve their environmental impact and optimise costs,” says Neil Pryke, James Heal MD. “Equipped with a unique water recirculation system, it is the only Bundesmann tester of its kind that reuses water during testing. This leads to significant environmental benefits and huge cost savings for our customers, without affecting the accuracy and reliability of test results.”
Established in Halifax, West Yorkshire in 1872, James Heal designs and manufactures textile testing instruments, which are used worldwide. The brand became part of the wider PPT Group in 2014, with a number of sister brands each focusing on testing many aspects of materials and products.
Business intelligence for the fibre, textiles and apparel industries: technologies, innovations, markets, investments, trade policy, sourcing, strategy...
Find out more