Starlinger rounds off portfolio with new circular loom RX 8.1
Technology/Machinery
Starlinger’s expanded range at ITMA 2019
At this year’s ITMA, Starlinger Group will present together with its new member STC Spinnzwirn for the first time.
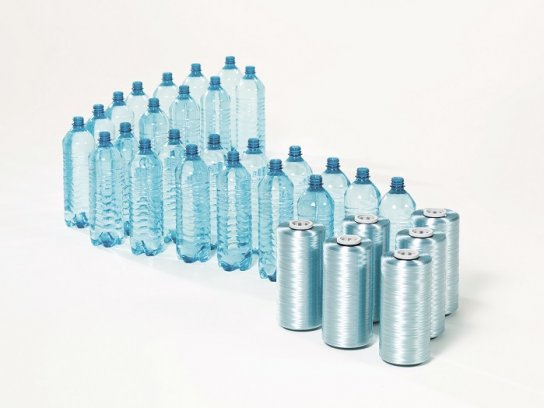
15th April 2019
Innovation in Textiles
|
Vienna
PET bottles are turned into tapes for plastic fabrics. © Starlinger
At this year’s ITMA, the world’s largest textile machinery exhibition held every four years, the Starlinger Group will present together with its new member STC Spinnzwirn for the first time. On a total area of 460 m², in Barcelona, this June, Starlinger will present its latest developments. The company, with headquarters in Austria, is a supplier of the entire product range for the production of plastic fabrics, from tape extrusion lines and circular looms through to sack conversion, plant monitoring, and the recycling of production scrap.
With the acquisition of the company now operating under the name STC Spinnzwirn (formerly known as Oerlikon business unit Barmag Spinnzwirn), Starlinger has expanded this broad range even further, particularly with respect to special extrusion (e.g., artificial grass, baler twine) and winding technology.
In addition to the winders and twisting machines of STC Spinnzwirn, ITMA visitors will be able to get a good impression of the Industry 4.0 solutions of winding specialist Georg Sahm, based in Eschwege, which joined Starlinger Group in 2002. Further ITMA highlights are the software solutions for central plant monitoring and digital process optimisation developed for the Starlinger Group by GRAFiT, a subsidiary founded in 2018.
PET bottles are turned into tapes for plastic fabrics. © Starlinger
With a focus on the circular economy, Starlinger will exhibit an FX 6.1 circular loom at ITMA 2019 to demonstrate the circular weaving of tapes made of recycled PET; the resulting rPET fabric is ideal for the manufacturing of U-panel FIBCs (flexible intermediate bulk containers or container sacks). The FX 6.1 is a 6-shuttle circular loom that is primarily used for the production of high-performance fabrics and does not possess any sliding parts which would require lubrication.
“This ensures that the fabric is completely oil-free and suitable for packaging food products,” the company explains.
Starlinger currently reports a high demand for circular looms with a large working width that are often used to make plastic fabric for FIBCs. Due to its form stability, flexibility and high melting point, (recycled) PET lends itself perfectly to FIBCs, in which large product quantities are transported and stored, according to the manufacturer. Further advantages of (r)PET FIBCs are their suitability for multiple use as well as recyclability.

Business intelligence for the fibre, textiles and apparel industries: technologies, innovations, markets, investments, trade policy, sourcing, strategy...
Find out more