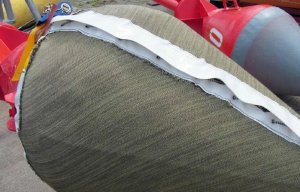
Cellulose and basalt innovations at Techtextil
Potential for the development of stronger, more sustainable, naturally derived plastics.
23rd February 2022
Innovation in Textiles
|
Cambridge, MA, USA
A team at MIT has engineered a composite made from 60-90% cellulose nanocrystals (CNCs) – the highest fraction achieved to date.
A single wood cell wall is constructed from fibres of cellulose and within each fibre are reinforcing CNCs – chains of organic polymers arranged in nearly perfect crystal patterns. At the nanoscale, CNCs are stronger and stiffer than Kevlar and if they could be worked into materials in significant fractions, they would prove to be stronger, more sustainable, naturally derived plastics.
The MIT researchers found the cellulose-based composite is stronger and tougher than some types of bone, and harder than typical aluminium alloys. The material has a brick-and-mortar microstructure that resembles nacre, the hard inner shell lining of some molluscs.
The team developed a recipe for the CNC-based composite that can be produced using both 3D printing and conventional casting. They printed and cast the composite into penny-sized pieces of film to test its strength and hardness and also machined the composite into the shape of a tooth to show that the material might one day be used to make cellulose-based dental implants that are stronger, tougher, and more sustainable.
“By creating composites with CNCs at high loading, we can give polymer-based materials mechanical properties they never had before,” said A. John Hart, professor of mechanical engineering. “If we can replace some petroleum-based plastic with naturally-derived cellulose, that’s arguably better for the planet as well.”
Each year, more than 10 billion tons of cellulose is synthesized from the bark, wood or leaves of plants. Most of this is used to manufacture paper and textiles, while a portion of it is processed into powder for use in food thickeners and cosmetics.
In recent years, scientists have explored uses for cellulose nanocrystals, which can be extracted from cellulose fibres via acid hydrolysis. The exceptionally strong crystals could be used as natural reinforcements in polymer-based materials but researchers have only been able to incorporate them at low fractions of CNCs because they tend to clump together and only weakly bond with polymer molecules.
Hart and his colleagues looked to develop a composite with a high fraction of CNCs that they could shape into strong, durable forms. They started by mixing a solution of synthetic polymer with commercially available CNC powder. The team determined the ratio of CNC and polymer that would turn the solution into a gel, with a consistency that could either be fed through the nozzle of a 3D printer or be poured into a mould to be cast. They then used an ultrasonic probe to break up any clumps of cellulose in the gel, making it more likely for the dispersed cellulose to form strong bonds with polymer molecules.
Some of the gel was fed through a 3D printer and the rest into a mould poured to be cast. They then let the printed samples dry. During subsequent drying, the material shrank, leaving behind a solid composite composed mainly of the cellulose nanocrystals.
Interestingly, when the team examined the composite’s structure under a microscope, they observed that grains of cellulose settled into a brick-and-mortar pattern, similar to the architecture of nacre. In nacre, this zig-zagging microstructure stops a crack from running straight through the material.
Tests were carried out on the material’s resistance to cracks and across multiple scales the composite’s arrangement of cellulose grains prevented the cracks from splitting the material. This resistance to plastic deformation gives the composite a hardness and stiffness at the boundary between conventional plastics and metals.
Going forward, the team is looking for ways to minimise the shrinkage of gels as they dry. While shrinkage isn’t much of a problem when printing small objects, anything bigger could buckle or crack as the composite dries.
This research was supported in part, by Proctor and Gamble and by the National Defense Science and Engineering Graduate Fellowship.
Business intelligence for the fibre, textiles and apparel industries: technologies, innovations, markets, investments, trade policy, sourcing, strategy...
Find out more