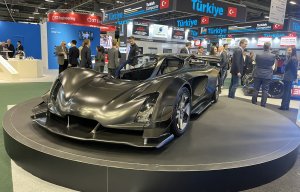
Glass fibre – the composites industry’s workhorse
Comprehensive LCA has validated environmental benefits and economic viability.
14th October 2024
Innovation in Textiles
|
Castellón, Spain
The four-year ZEBRA project is concluding this month, having successfully demonstrated and validated two recyclable thermoplastic wind turbine blades.
The second blade, measuring 77 metres in length, was completed at LM Wind Power’s plant in Castellón, Spain, in December last year, using Arkema’s thermoplastic Elium liquid resins and Owens Corning high performance glass fabrics. It also features a new carbon-Elium resin spar cap technology and benefits from a new Arkena adhesive.
The second ZEBRA blade is a world-first in using recycled Elium resin in the manufacture of a shear web, which is a structurally important component of the blade, and demonstrates the potential of the resin technology to deliver sustainable blade designs.
“The second ZEBRA blade builds on the learnings and valuable insights gained from the creation of the first blade and has helped us understand the structural potential to use Elium resin in carbon blades,” said John Korsgaard, senior director at LM Wind Power. “It complements the efforts led by our partners to demonstrate the recycling technologies for Elium-based composites using glass and even carbon fibre. This blade marks a key milestone for the ZEBRA project and highlights the significance of plant collaboration in new technology development.”
Launched in September 2020, the ZEBRA project is a unique partnership which has been led by French research centre IRT Jules Verne and brought together industrial companies Arkema, Canoe, Engie, LM Wind Power, Owens Corning and Suez.
Each company played a crucial role in the development of the closed-loop recycling proces.
Arkema developed and validated the generation of recycled Elium monomer through thermolysis and together with its subsidiary Bostik also made the new adhesive for the blade assembly that is recycled together with Elium, paving the way for industrial-scale implementation.
Owens Corning successfully recovered glass fibre at pilot scale, enabling its reintroduction into the production process for its Sustaina product line. Suez provided cutting and grinding expertise for processing the blades and the Canoe R&D centre optimised recycling for production and carbon blade waste, additionally developing methods for repurposing waste streams through mechanical recycling.
Engie conducted the comprehensive life cycle analysis demonstrating the environmental benefits of closed-loop ZEBRA blades and validated their economic viability.
Business intelligence for the fibre, textiles and apparel industries: technologies, innovations, markets, investments, trade policy, sourcing, strategy...
Find out more