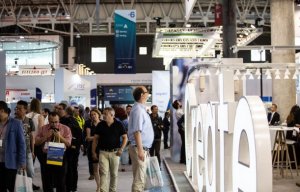
CEMATEX introduces online platform for ITMA
Nonwovens manufacturers were the very first textile recyclers, and in the next few years their services will be needed more than ever.
28th November 2024
Innovation in Textiles
|
Singapore
In the latest live webinar from ITMAconnect which will be broadcast on December 5th, Claire Mattelet, sustainable programs director at Indorama Ventures and Dr Jeff Strahan, director of research, compliance and sustainability for Milliken, will outline the closed-loop recycling solutions, biotransformation technologies and strategies for carbon footprint reduction being developed by their companies.
Indorama’s innovations include thermomechanical and chemical recycling technologies, bio-based raw materials and additives for the end of life biodegradability of polyolefins
Strahan will meanwhile provide details of Milliken’s verified net-zero goals and the role of carbon pricing in driving sustainability.
With a focus on recycling technologies, energy efficiency and sourcing recycled materials, the webinar will highlights how nonwovens are paving the way to a net zero future.
First recyclers
Nonwovens manufacturers were the very first textile recyclers, and in the next few years their services will be needed more than ever.
The European Union is introducing a ban on the landfilling or incineration of post-consumer clothing waste beginning in January 2025 and will impose an extended producer responsibility (EPR) scheme on brands and manufacturers to pay for its collection and disposal. The European Commission is further calling for all textile products on the EU market to be durable, repairable or recyclable – and to contain a significant percentage of recycled fibres – by 2030. Similar legislation is expected to follow elsewhere in the world.
Second life
The nonwovens industry already mechanically recycles a lot of textile waste into second life products such as insulation for the automotive and construction industries, industrial wipes and mattress covers, but to date this has been largely from regenerated mill waste fibres.
Mill waste fibres are comparatively pure compared to post-consumer apparel waste, where many finished articles are often based on blended fibres – most commonly of polyester and cotton – with elastanes, chemical finishes and many other impurities such as buttons, zips and linings to be removed before a bale of fibres can be shipped for reprocessing.
As a consequence, today’s mill waste is going to be much more valuable going forward, as the apparel brands look for recycled feedstocks that can be incoroprated into their their clothing ranges that are produced by the conventional routes of yarn spinning, followed by weaving or knitting.
Short fibres
The successful spinning and further processing of recycled staple fibres in conventional textile processing, however, is very much dependent on their purity and length, and short fibres are always problematic. Bales of virgin cotton, for example, have an average short-fibre content of 25%, but short-fibre content in recycled yarn waste from mills is on average 47%, which already makes turning it into new yarns for spinning challenging.
Post-consumer waste has a much higher percentage of short staple fibres, amplifying the problem.
At best, it is estimated that textile apparel containing 40% post-consumer waste fibres is the current limit to be achieved in staple fibre blends with virgin fibres for spinning – nonwovens manufacturers are already achieving 100% recycled content in many high-value products.
Key ITMA exhibitors specialising in mechanical recycling systems for nonwovens production include, among others, Andritz Laroche, Balkan, Bonino, Dell’Orco and Villani, Masisas and Temsan.
Mechanical recycling, however, still has limitations in terms of the type of fibres that can be accommodated and the volumes that will need to be achieved to meet legislative requirements.
As consequence, chemical recycling is now gaining momentum as a huge new industry sector, especially targeting polyester, as the predominant synthetic fibre employed in textiles.
In this area, it is notable that only a handful of companies are working to regenerate pure chemical polymers, rather than taking fibres right back to the chemical monomers they are composed of, for use as new feedstocks.
Synthetic waste polyester and other synthetic fibre waste can be turned back into monomers by four major methods – methanolysis, glycolysis, hydrolysis and enzymatic recovery.
Many major nonwovens manufacturers using synthetic fibres have been swift to recognise this trend and opted to become ISCC PLUS certified as a means of proving their achievements in accommodating recycled content – in the form of initial feedstock chemicals – in their products.
Further details
The ITMAconnect webinar, Sustainable Nonwovens: From Transformational Technology to a Net Zero Future, is open to all and will be broadcast from 2.30-3.30pm CET on December 5th. It will be chaired by Dr Behnam Pourdeyhimi executive director and associate dean at the North Carolina-based Nonwovens Institute.
Registration details can be accessed here.
Business intelligence for the fibre, textiles and apparel industries: technologies, innovations, markets, investments, trade policy, sourcing, strategy...
Find out more