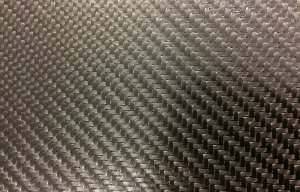
Improved dimensional accuracy with RP800
Input from spinning mills is applied with each software update of the Jossi Vision Shield.
16th December 2021
Innovation in Textiles
|
Uster, Switzerland
Uster reports that ongoing dialogue with customers ensures spinning mills play a continuing role in the development of its system improvements.
Customer needs are fed back directly to Uster R&D experts, leading to constant progress in fibre cleaning, with reductions in costs, less waste and a stress-free experience for the spinners.
Over 2,000 Uster Jossi Vision Shield installations in spinning mill blowrooms around the globe, for example, testify to its success, but Uster development teams continue to explore further improvements.
The detection capabilities of the Jossi Vision Shield come from its sensors and powerful imaging recognition technology with which the smallest particle of contaminant will be picked out,.
Such detection performance might make some spinners nervous that too much good cotton could be ejected with the contaminants. However, the system’s speed measurement feature actually provides a notable reduction in waste. By continuously measuring the velocity of the passing cotton tufts, it can adapt the duration of each ejection, so that a minimum of material is removed with the contaminant. Mill trials have proved that optimising ejection times in this way results in significantly less waste per ejection.
In the highest quality segment, fibre cleaning settings can be set to even tighter tolerances, without increasing waste. For less critical applications, spinners can retain existing quality settings and see waste greatly reduced, with fewer ejections. In all cases, mills can expect significant improvements in the balance between quality and efficiency.
Information flow
The software built into Jossi Vision Shield is also under continuous improvement and algorithms are adapted to take account of customer feedback,
One example of the impact of this is the “Laydown Change Button”. Spinners based in various markets requested the facility to mark the change-over time for a new laydown. The new feature helps with this, and also allows statistical data to be aggregated correctly.
A solution to reduce the downtime of products and several enhancements to software have also resulted from customer obervations and contributed to the overall stability of the system.
“The input of our customers is applied with each software update as part of our success model,” says Suresh Kris, vice-president global after sales and service.
Business intelligence for the fibre, textiles and apparel industries: technologies, innovations, markets, investments, trade policy, sourcing, strategy...
Find out more