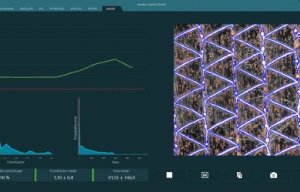
Effective analysis from Apodius
Tiniest contaminants in the melt can cause production problems.
25th June 2021
Innovation in Textiles
|
Linz, Austria
IFG Asota, based in Linz, Austria, is the R&D centre of the Industrial Fibres Group (IFG), a leading European manufacturer of melt-spun polypropylene, polyethylene and polyamide staple fibres.
Due to the many different in-house and customer-oriented challenges in the development of specialities for specific applications – and increasingly also from biopolymers such as PLA (polylactide) and PBS (polybutylene succinate) – product changes are very frequent on the semi-industrial pilot plant installed at the Linz site.
Thorough cleaning of the two extruders keeps the time needed for this and the amount of material required to a minimum, and also contributes considerably to the high quality of the fibres produced.
Dreyclean LT high-performance cleaning granulates from Dreychem have proved to be an optimum choice for this task.
“With the fibre diameters down to less than 20 µm, even the tiniest contaminants in the melt can cause production problems,” says Andreas Weinberger, R&D manager at IFG Asota. “In particular, when the machine has been idle for a certain time, rinsing with the usual polymer is not enough to reliably remove all the deposits and agglomerates. This applies all the more to biopolymers, which rapidly tend to thermal degradation at elevated temperatures. Here, the cleaning granulates from Dreychem have proved to be so efficient that since we started using them, we have had significantly fewer problems such as fibre breakages. In addition, our experience shows that following their use, processing temperatures in the extruder of up to 20°C lower are sufficient for achieving the same throughput. This improves the quality of the biobased fibres and lowers the energy consumption.”
Another particular benefit of using Dreyclean LT, he adds, is the much lower material loss compared with rinsing with the original material.
“Biobased plastics such as PLA are much more expensive than conventional thermoplastics used for melt spinning. This, plus our overall shorter running times per batch, make the material losses until a stable process is reached a significant economic factor. With Dreyclean, we have been able to cut this start-up time by more than half.”
“With Dreyclean LT, we have developed a mechanically acting cleaning granulate that is able to eliminate particularly stubborn incrustations and other deposits very effectively indeed, without any abrasive ingredients in the recipe,” says Kerstin Brunken, managing director of Dreychem. “The standard range of application extends from polyolefins through PET to TPE and TPU at processing temperatures of 180 to 320 °C, in extrusion and also when cleaning injection moulding machines and tools. We are delighted that the product’s application at IFG Asota now also proves the beneficial effect when processing biopolymers.”
Business intelligence for the fibre, textiles and apparel industries: technologies, innovations, markets, investments, trade policy, sourcing, strategy...
Find out more