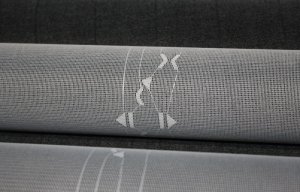
Textile-circuit from Karl Mayer
Warp knitted textiles combine the stability of woven fabrics with the elasticity of knitwear, according to warp knitting machine manufacturer Karl Mayer
25th September 2020
Innovation in Textiles
|
Obertshausen
Warp knitted textiles combine the stability of woven fabrics with the elasticity of knitwear, according to warp knitting machine manufacturer Karl Mayer. Different thread systems can also be combined with warp knitting technology to produce fabrics with a wide variety of properties, the company adds, and functional yarns in particular can result in exceptional performance profiles.
Karl Mayer reports it has already carried out extensive development work in this field, in which electrically conductive and high tenacity materials were processed on multibar raschel machines. For some time now, the high-performance machines have been making new, chic lace patterns possible for the lingerie and clothing sector. When producing technical fabrics, functional yarns can be arranged in areas of any shape, size and placement thanks to their diverse potential, Karl Mayer explains.
Multiple patterns with multibar
A combination of jacquard and multibar patterning is the prerequisite for the extraordinary patterning possibilities of multibar raschel machines, the company says. The split jacquard bars are full set threading and produce a basic structure that can be creatively designed using a single needle motion, while string bars with multibar patterning incorporate additional yarns into the diverse ground structure to add a functionality. The added thread material is supplied by bobbins, so it does not have to be warped onto warp beams.
The smart path to electrically conductive textiles
By directly integrating electrically conductive yarns into warp knitted textiles, functional elements such as sensors, conductors and coils can be incorporated very easily, without any additional production steps or compromising the textile characteristics, Karl Mayer clarifies.
Karl Mayer’s Product Manager, Sophia Krinner, has already investigated the possibilities as part of Textile-Circuit. Silver coated filaments such as ELITEX, Silvertech, Shieldex and Agsis were used for the work. Even fine insulated metal filaments and metallized yarns like ELITEX TPU and Percon isolated can be used – depending on flexibility and diameter.
In general, Karl Mayer says, the yarns must be matched to the properties of the desired textile and to the machine gauge in terms of bending stiffness and radius. Only minimal adjustments to the conventional multibar raschel model used for the work were necessary.
Non-insulated filament yarns can be used on current machines with additional voltage monitoring, and a specific modification of the yarn guiding is recommended when using insulated metal filaments. Previous results of work carried out as part of Textile-Circuit include arm sleeves to conveniently control robots, textile charging stations with coils of electrically conductive yarns to inductively charge smartphones and a sports shirt with integrated sensors to measure heart rate, temperature and humidity. The clothing solution that uses a Bluetooth-enabled app for communication was demonstrated live at ITMA 2019 in Barcelona. This was followed by work to optimise the solution further, resulting in an electrode with a soft 3D shape that offers more skin contact and thus delivers a better signal. This makes it possible to create clothing with a looser, more comfortable fit, while the electronics are smaller and thus offer greater scope for design.
High tenacity yarns placed to reinforce buttonholes
In addition to electrically conductive yarns, Sophia Krinner conducted a basic test to process high tenacity materials on the string bars of multibar raschel machines. Using functional thread variants, different structures to reinforce holes were created; the yarns used had counts of 880 to 1880 dtex and specified strength between 35.1 and 5 cN/dtex. They were used on a gauge E 18 machine together with polyamide 6.6 as base material.
The entire structure of the produced fabrics was tested in terms of tear resistance. The tests were based on the standardised grab tensile test and an in-house test used for measuring the hole tensile strength. In her evaluations, Sophia Krinner always compared the results to that of pure basic fabric made from standard polyamide. The tensile strength was significantly lower across all test specimens than that of the pure high tenacity material, since the base fabric always gave way first. However, Karl Mayer explains, compared to the basic fabric made from pure polyamide, strength values were significantly improved by all the functional materials used. In the most extreme cases, the whole tear resistance of the basic structure could be quintupled by individually placed, high-strength weft threads, and the tensile strength of the fabric increased eightfold.
Committed development partner with ideas
Karl Mayer says it counts on the synergetic combination of the textile sector and new technologies to launch related activities that are brought together and coordinated in its Textile Makerspace. The focus here is on the Textile-Circuit and Rapid Textile segments.
Textile-Circuit demonstrates the possibilities of incorporating electrically conductive yarns into warp knitted textiles directly on the machine, while Rapid Textile focuses on the topic of additive manufacturing, particularly the combination of 3D printing with textile technology.
The latest developments in this area point to new production methods for the footwear industry, the German machine manufacturer says. The work towards this, involved printing functional elements such as reinforcing structures onto stretched fabric. When relaxed, the 3D prints ensure that the upper creates the required shape, without the need for moulding.
With its commitment to the Textile Makerspace, Karl Mayer supports the development of innovative textile products. The company is also working to ensure that functional textiles can be produced economically in industrial processes. To do so, it uses technology that offers a variety of advantages. Warp knitting is as fast as it is versatile, Karl Mayer adds. It enables functional materials to be incorporated directly on the machine in line with the application and results in products with typical textile properties such as softness, elasticity, flexibility and breathability, the company concludes.
Business intelligence for the fibre, textiles and apparel industries: technologies, innovations, markets, investments, trade policy, sourcing, strategy...
Find out more