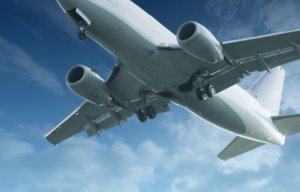
Attwater secures its transition to AS9100D
Older hydraulic system lacked the speed and accuracy of control needed.
7th October 2021
Innovation in Textiles
|
Huddersfield, United Kingdom
A new control system featuring an ABB variable speed drive (VSD) is efficiently managing the tension control and changing the size of the fabric reel as it traverses through dyeing processes for DP Dyers, based in Huddersfield, UK.
The VSD’s in-built PID (proportional-integral-derivative) loop allows the system to automatically match torque to the requirements of the running fabric based on the thickness and number of wraps
The DP Dyers machine – known as a jigger – comprises a winder that feeds the fabric into the dye and a rewinder that gathers the finished product. The winder and rewinder were previously both controlled by an ageing hydraulic system, the motors of which suffered regular breakdowns. The hydraulics lacked the speed and accuracy of control needed by the winder/rewinder, resulting in uneven dye distribution.
A 5.5 kW ABB industrial drive was recommended by Halcyon Drives, a member of the ABB Value Provider network based in Warrington, UK. The VSD ensures a uniform dyeing or bleaching process by maintaining a constant tension in the wound fabric as the diameter of the reel changes.
The VSD uses its in-built PID loop to calculate the torque needed to manage the tension of the fabric running between the winder and rewinder. Meanwhile, the VSD determines the required speed of winding based on the material thickness and the number of turns of fabric, or wraps, on the lead roller. The system drives the fabric onto a roller and counts the number of wraps. The operator measures from the outside wrap to the core and inputs this to the VSD, which then calculates the fabric thickness based on the outside diameter divided by the number of wraps.
“We are getting a much more consistent product with more even dyeing due to the VSD, which constantly adjusts the web speed and torque to maintain the correct tension,” said Robert Clay, site engineer at DP Dyers. “The control system is now much more user friendly, with the software giving the alarm history of jobs. Now we have much more data, showing a history of temperatures and times of operation.”
Prior to installing the VSD, the machine’s weekly energy consumption was typically 597 kWhr costing around £50. Following installation, this reduced to 169 kWhr and £14 respectively – a reduction of around 70%.
By connecting software to its electrification, robotics, automation and motion portfolio, ABB is pushing the boundaries of technology to drive performance to new levels. With a history of excellence stretching back more than 130 years, ABB’s success is driven by 105,000 employees in over 100 countries.
Business intelligence for the fibre, textiles and apparel industries: technologies, innovations, markets, investments, trade policy, sourcing, strategy...
Find out more