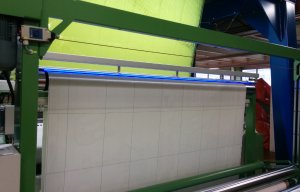
Pushing the boundaries of fabric inspection
MES (manufacturing execution system) offers full control of the entire production flow.
4th March 2021
Innovation in Textiles
|
Belgium
As part of Pakistan’s vertically integrated Sapphire Group, denim manufacturer Diamond Fabrics has partnered with Belgium-based BMSvision for the implementation of a new manufacturing execution system (MES), on the road to becoming an Industry 4.0 company.
“We were looking for a solution that went far beyond the traditional production and machine monitoring and needed an MES system that could manage and track the entire production flow, from yarn to finished fabric,” explained Diamond’s Tayyab Abdullah. “Furthermore, it needed to seamlessly integrate with the SAP enterprise resource planning system in place. After thorough market research and various demonstrations and workshops, we selected BMSvision as our partner because of their vast experience in the industry and the turnkey project approach including hardware, software and services they take.”
BMSvision is taking a turnkey project approach, including the provision of hardware, software and services
A first phase of the project covers the warp preparation department including ball warping, sizing and rebeaming, as well as the complete denim finishing department. These are the most challenging operations within a denim mill.
In a second phase, all looms will be connected. Each machine in the preparation and finishing departments is equipped with a state-of-the-art touch screen based DU11 data collection terminal with wireless barcode scanner.
Scheduling
Once the production orders are released by the SAP system, the planning department uses the BMSvision scheduling software (PlanBoard) to assign the orders to the individual machines. Orders are started at the machine by scanning the barcoded batch travel card.
The PlantView application visualizes the complete production process in real time and highlights any possible deviation from standard. A powerful reporting tool featuring interactive reports and charts allows users to create their own calculations and reports. After each production step, the MES systems prints a barcoded ticket and all relevant production data is transferred to the SAP system.
Diamond’s request to monitor and document the flow of goods throughout the whole production chain, to be able to trace all materials used and to know the current Work in Process status all the time, is handled by BMSvision’s traceability module.
EnergyMaster
In addition to managing the production flow, Diamond Denim also implements the BMSvision EnergyMaster solution.
“Energy consumption is becoming a very important factor in the overall operating cost of our factory,” said Tayyab Abdullah. “With ever rising energy prices and increasing environmental legislation, energy management has become a critical success factor to run our business in a profitable way.”
The EnergyMaster system makes all our energy streams transparent and allows us to allocate the exact energy cost to each production batch.”
The finishing lines are equipped with power meters and various flow meters to monitor the consumption of compressed air, steam, water, gas, and caustic. All these meters are connected to the DU11 data collection terminal and combining consumption with production data allows correct calculation of the energy cost for each production batch. Excessive consumption or consumption while the machine is idle are immediately detected and highlighted.
Business intelligence for the fibre, textiles and apparel industries: technologies, innovations, markets, investments, trade policy, sourcing, strategy...
Find out more