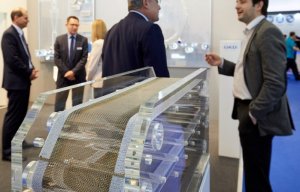
GKD process belt innovations prove a hit at Techtextil
Oven belts made of glass hybrid fabric are said to be setting new benchmarks in the production of nonwovens.
27th November 2019
Innovation in Textiles
|
Düren
In exacting thermal bonding processes, the antistick coated glass hybrid fabric belts from GKD are said to offer better process performance and product quality than glass gauze belts. © GKD
After more than three years of practical application, the results have significantly exceeded the high expectations: In exacting thermal bonding processes, the innovative glass hybrid fabric belts from GKD - Gebr. Kufferath (GKD) are said to offer “impressive process performance and product quality”.
More and more users are now choosing this type of belt – which was initially predominantly used as a magnetic upper belt in double-belt dryers – as well as a lower belt. Its completely PFA-coated construction of glass strands in the running direction and metal wires in the weft is designed to prevent adhesions of adhesive products. This is said to minimise cleaning intervals and downtimes, while the production speed and tool life far exceed conventional benchmarks.
Weighing 1.8 kg per square metre, this innovative belt construction from the leading international technical weavers GKD is an energy-efficient lightweight in dryer operation. At the same time, the material combination of metal and fiberglass increases process efficiency thanks to its highly resistant PFA-coating, according to the manufacturer.
“Even when using BiCo fibres, it reliably protects the wires and the intersections between the chain and weft against adhesions. Neither fibres nor binders are deposited in the fiberglass strands or between the wires. This minimised soiling means production speeds can be significantly increased,” the company reports.
The anti-stick coated glass hybrid fabric belts from GKD have proven their worth as a sustainable, economic solution for thermal bonding processes. © GKD
“The high transverse stability of this type of belt is crucial in optimising the process quality and product quality: Even for products with large weaving widths or strong shrinkage forces, the single-ply belt construction impresses thanks to its excellent running properties. In the upper belt, magnetic steel weft wires, which are over 0.8 mm thick, reliably hold the belt on the magnetic strips. The resulting absolute flatness guarantees exact calibration and compression. When used as a lower belt, a stainless steel weft wire guarantees similar transverse stability. Even highly voluminous and significantly compacted products obtain a constant thickness and density over the entire width, with minimal tolerances.”
Glass hybrid belts by GKD are characterised by an even mesh opening with high air permeability. The fiberglass strands are temperature resistant up to 250 degrees C, thus preventing belt elongation. In addition, the intricate PTFE edge coating also makes the belts more durable: This very smooth and absolutely straight cut edge makes reliable belt control easier.
Glass hybrid belts by GKD are characterised by an even mesh opening with high air permeability. © GKD
Furthermore, the sewn, non-marking pin seam is said to guarantee impression-free production of nonwovens. The growing demand for use as the upper and lower belt is a striking reflection of all the advantages of GKD glass hybrid belts. Initially installed by plant manufacturers as the upper belt in dryers, these belts have been running since 2016 and have far exceeded the expectations of the first users, the company reports.
Compared to glass gauze belts, which often only last for a few months in wide thermal bonding plants, the years of runtime provided by glass hybrid belts have compensated for the higher procurement price several times over during the first year alone. The result is that more and more users have installed this type of belt as the lower belt too, where it has been running with great success for about a year and a half. “So, overall, GKD's glass hybrid belts have proven their worth as a sustainable, economic solution for thermal bonding processes due to their durability, increased productivity, minimized cleaning intervals and higher production speeds – with better product quality to boot,” the manufacturer concludes.
Business intelligence for the fibre, textiles and apparel industries: technologies, innovations, markets, investments, trade policy, sourcing, strategy...
Find out more