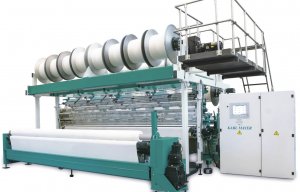
Less twist, more comfort and durability
Sustainability is becoming increasingly important in textiles production – and this also applies to the production of warp-knitted terry fabrics.
6th August 2018
Innovation in Textiles
|
Obertshausen
Sustainability and environmental protection are becoming increasingly important in textiles production – and this also applies to the production of warp-knitted terry fabrics. These fluffy, absorbent fabrics are absolutely indispensable for the bathroom and home and are used in huge volumes all over the world. This means that ecological optimisation, carried out along the entire production line, has obvious effects.
Leading German warp knitting machinery manufacturer Karl Mayer supplies Prosize sizing machine that can offer advantages for the environmental footprint of the entire manufacturing process when producing woven terry goods.
This warp preparation machine operates on the basis of a prewetting principle, which involves soaking the yarn with hot water before the size is applied. “This permits savings of up to 40% to be made in sizing additives and energy,” the manufacturer explains.
“This principle is simple yet effective: the water penetrates into the hollow spaces of the fibrous structure and partially fills them once the excess water has been squeezed out. During subsequent sizing, the water in the damp yarn rapidly forms a bond with the size. The textile agent is, therefore, absorbed more rapidly and easily by the warp yarns than with processes that do not involve prewetting. On the other hand, the diluting effect of the water in the yarn structure ensures that most of the size remains on the fibre surface. This reduces the consumption of chemicals.”
To carry out this beneficial pretreatment process, the Prosize has been equipped with the HSB-PW size box, i.e. it is available as a prewetting version.
The innovative size box is also said to deliver ecological advantages for the sizing process itself. Instead of the usual immersion and bath application process, the size is applied in three, highly turbulent, homogeneous application zones, with spray bar technology and a subsequent application/squeeze roller system. This processing sequence can reduce the consumption of sizing agent by up to 10%. Reduced size consumption also means less effluent and a lower energy consumption when preparing the chemicals for application to the yarns, the company explains.
The spray technology also offers advantages in terms of conserving resources, since yarn rejects as a result of long machine stoppages are minimised. With the immersion process, if the machine is stopped, the yarns remain in this position in the size. Over-sized sections, so-called stop marks, are produced, which cause problems with rejects during subsequent sizing and weaving – and this is even more of a disadvantage during frequent and rapid warp changes.
Karl Mayer can supply the TM 4 TS-EL for producing warp-knitted terry fabrics. This four-bar tricot machine processes staple-fibre yarns and produces high-quality textiles, in which the terry loops are firmly anchored into the ground during the stitch-forming process. The pull-out resistance of the loops is much higher than that of comparable woven fabrics. Warp-knitted towels and bathrobes can, therefore, be used for longer, which generates less waste. The longer replacement cycles also reduce the consumption of resources.
Warp knitting also scores points for sustainability during fabric production. The TM 4 TS-EL is said to consume roughly 87% less energy per kg of fabric produced than airjet weaving machines, which require large amounts of energy to produce the compressed air. This advantage is also enhanced by the high efficiency of this terry warp knitting machine. At a width of 186'' and a speed of 800 min−1, the TM 4 TS-EL has a daily production rate of about 1,800 kg of terry fabrics with a weight of 400 g/m2 - 250% more than on an airjet weaving machine, according to Karl Mayer.
Following a long gap in what was available in the range, the TM 4 TS-EL was premiered at ShanghaiTex 2015 as a new terry warp knitting machine for processing cotton. Thanks to the modern EL pattern drive system, the speed of the TM 4 TS-EL has been increased by about 30% compared to its predecessor with manual transmission. A working width of 186" has increased output even further.
The machine can produce every type of terry article, especially hand and bath towels, i.e. webs having long repeats, smooth ends to the borders, and cutting edges. The EL system also enables the pattern to be changed quickly and easily.
Business intelligence for the fibre, textiles and apparel industries: technologies, innovations, markets, investments, trade policy, sourcing, strategy...
Find out more